Three countries and 3,000 km: delivery of another lot of equipment to Nizhnekamskneftekhim’s ethylene plant
The sixth ship with large equipment for Nizhnekamskneftekhim’s new EP-600 plant has arrived at Nizhnekamsk’s cargo port. Covering 3,000 kilometres, Neva-Leader 2 has delivered 61 pieces of manufacturing equipment to the petrochemical capital of Tatarstan. A part of the equipment was loaded in Italy, the other part was in Romania. Read more in Realnoe Vremya’s report.
From Marghera to Nizhnekamsk
Neva-Leader 2 ship is considered to be one of the biggest for the Russian river system. Its length reaches almost 140 metres, the width is 16,5 metres, the height is 13 metres. The next lot for Nizhnekamskneftekhim’s new ethylene plant arrived precisely on its board. The steamship’s journey began in the north of the Adriatic Sea.
“We pull out from Marghera in Italy. Then we went to Romania. We have covered 3,000 kilometres in total. The journey went through Roston-on-Don, the Don, Volga and Kama rivers. Traffic is being heavy in the Volga-Don Canal now. Almost no water left in the river canal because of gale-force winds, a lot of ships have accumulated. Navigation is coming to an end, everybody is trying to deliver freight. There weren’t such problems anymore when we were crossing the Volga,” says Vladimir Moiseyev, captain of Neva-Leader 2.
The trip from Marghera to Nizhnekamsk took about three weeks. The ship arrived in Tatarstan a week late. According to specialists, bad weather influenced only the duration of the trip, not the course of construction of Nizhnekamskneftekhim’s ethylene complex. All the main manufacturing equipment whose assembly is running full steam was delivered to the construction site earlier. Neva-Leader 2 ship brought another 61 pieces of equipment to Nizhnekamsk. Its assembly will start according to schedule.
“There is different equipment on board. There are heat exchangers, 15 pieces of equipment was loaded onboard in Italy. Another 46 pieces of equipment delivered from South Korea was loaded in Constanţa, in Romania,” said Viktor Krinitsky, coordinator of Deugro Project.
264 pieces of equipment in total during this navigation period
Roads were expanded, obstacles on the way were removed, temporary structures were built to deliver the columns to the construction site. The equipment is transported with the help of special cranes and machinery.
“The transportation of this equipment will take three days. We agreed with Nizhnekamskneftekhim on the deployment plan and equipment delivery. The petrochemists said where and how it will be stored. We are planning to have seven runs every day. There will be used special machinery: breakdown trucks, trailers, semi-trailers. There were special requirements for the transportation of the convection unit. It is considered sensitive equipment, this is why it was decided to use hydraulic trailers that can lift about 300 tonnes,” says Sergey Rutman, a manager of Deugro Project.
It is planned to deliver 264 pieces of equipment in total during this navigation season. The next ship with valuable freight on board will arrive in Nizhnekamsk these days already.
“There will be another ship. We’re expecting it on 22-24 October. It will be the last ship during this navigation season. We hope it will arrive without delay. The ship has already passed by Rostov-on-Don and is going towards Nizhnekamsk. It has another 58 pieces of large equipment on board,” noted Viktor Krinitsky, coordinator of Deugro Project.
“The new complex will cement the status as a big market player in Russia and CIS countries”
The construction of Russia’s unique ethylene plant with a capacity of 600,000 tonnes kicked off in February 2019. The implementation of the project is conditioned by a strategy of Nizhnekamskneftekhim PJSC. The new complex will cement the status as a big market player in Russia and CIS countries, increase the production of target products with a high added value. The plant will refine 1,798,500 tonnes of naphtha a year and make 600,000 tonnes of ethylene, 272,800 tonnes of propylene a year, 88,000 tonnes of butadiene a year, 245,000 tonnes of benzene a year.
Modern ideas of crude hydrocarbon refining will be used in the complex. It is planned to build local treatment facilities where sewage generated in production will be treated and reused. This will minimise the environmental impact and reduce consumption of clarified river water from the Kama River. Emissions of harmful substances will reduce four times compared to analogous plants. An up-to-date flare system will be installed in the facility.
Germany’s Linde is the designer of the project and engineering documentation of the new EP-600 plant. Turkish Gemont company is the contractor general of construction and assembly works.
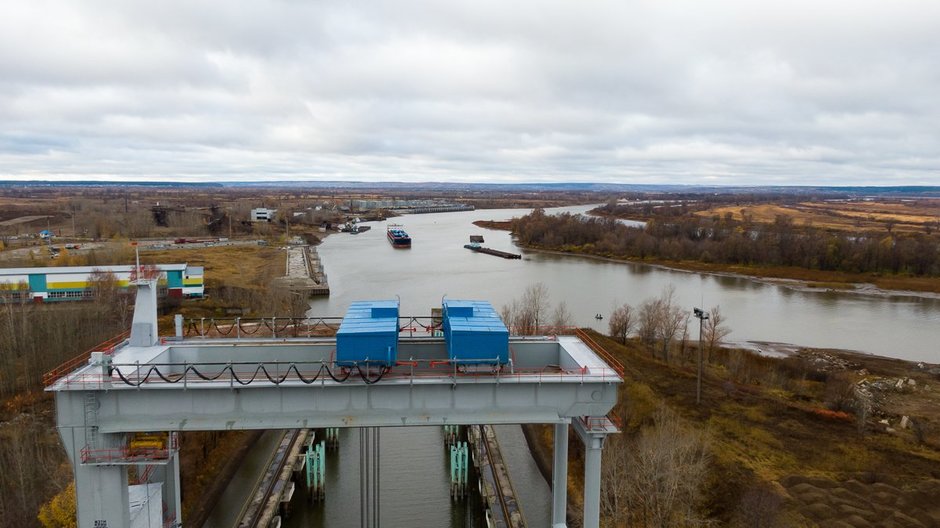
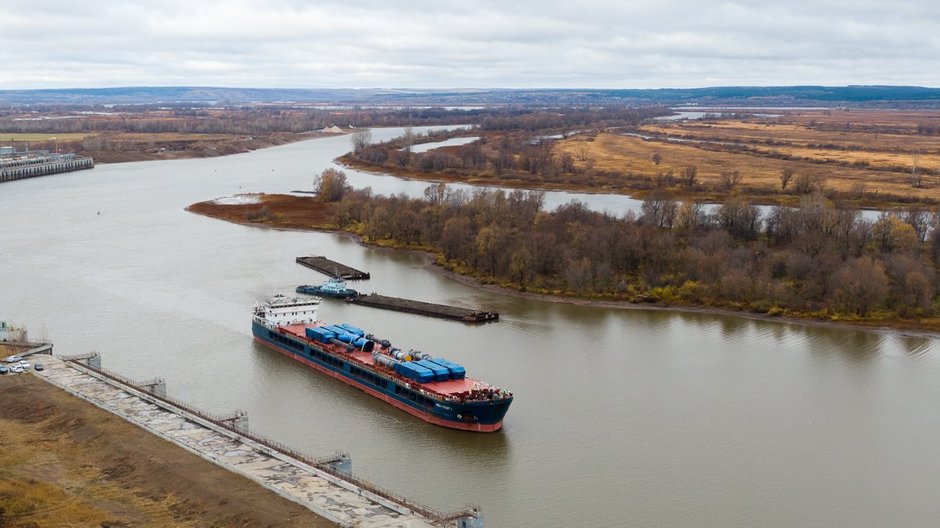
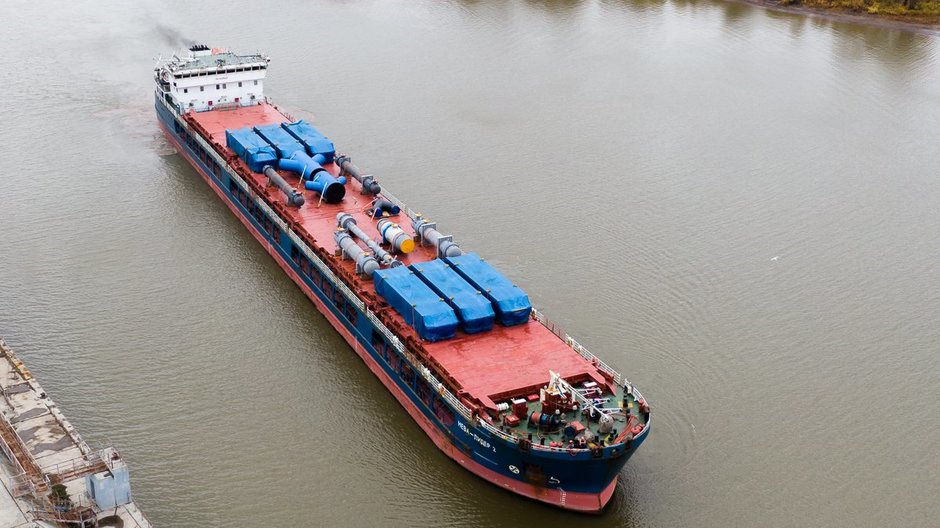
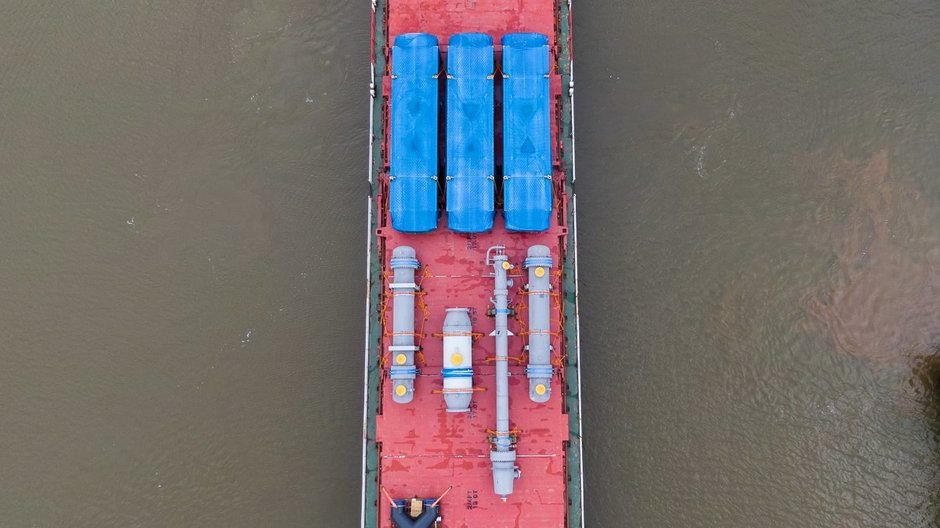
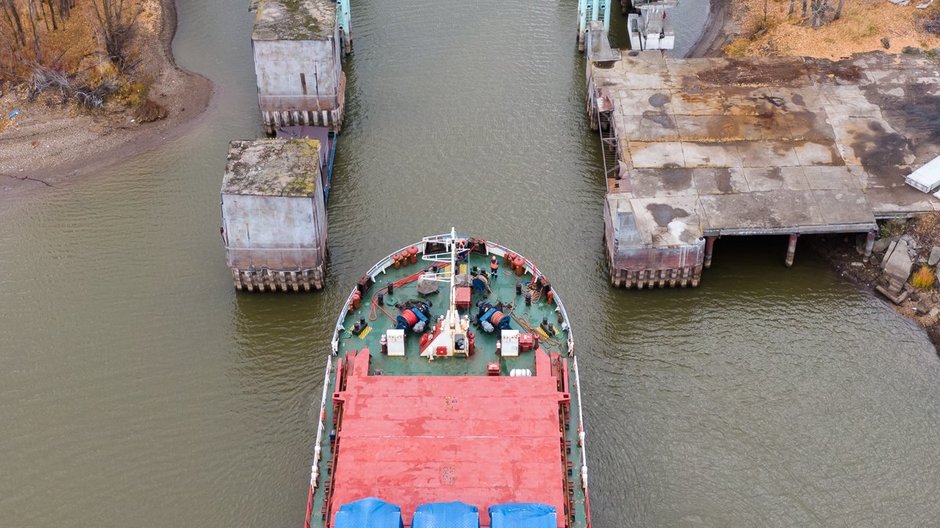
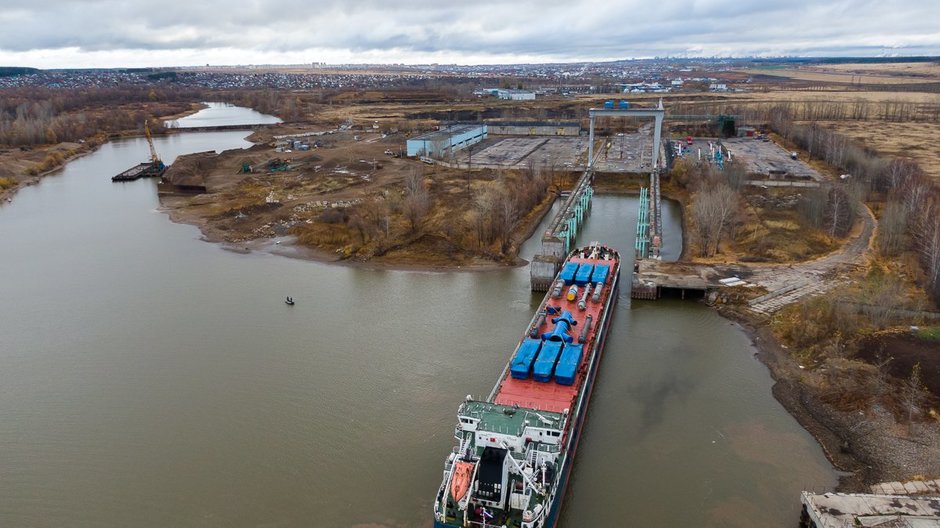
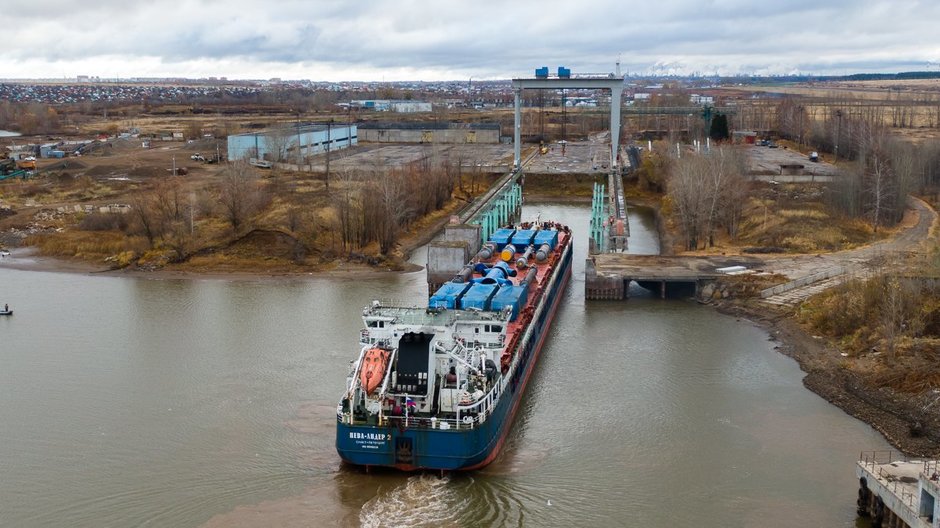
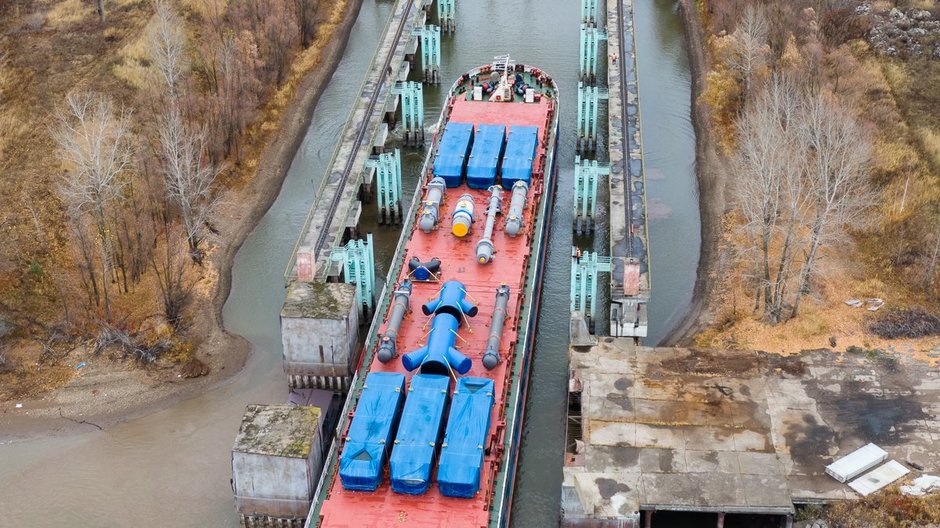
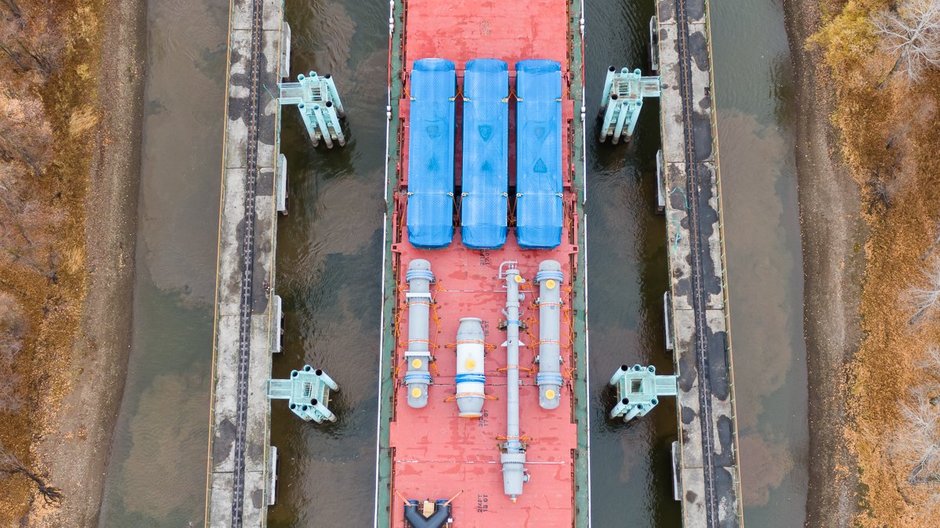
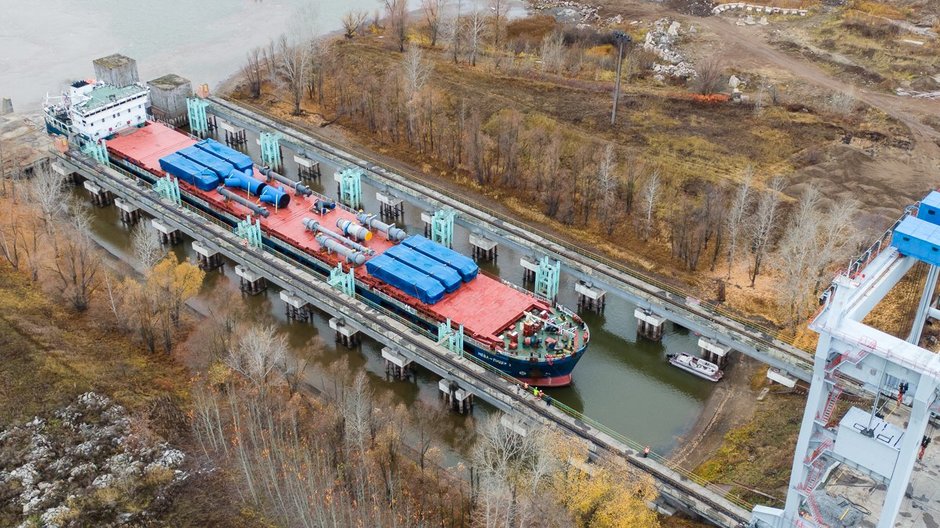
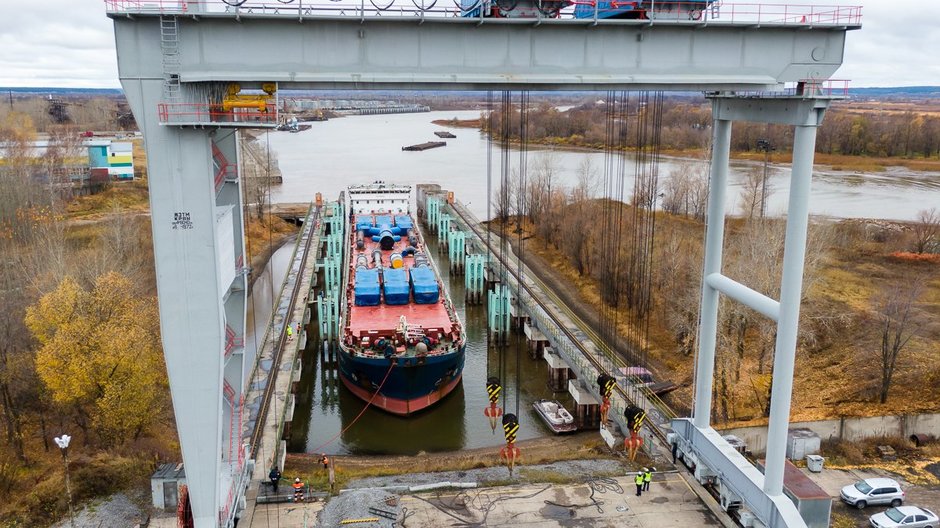
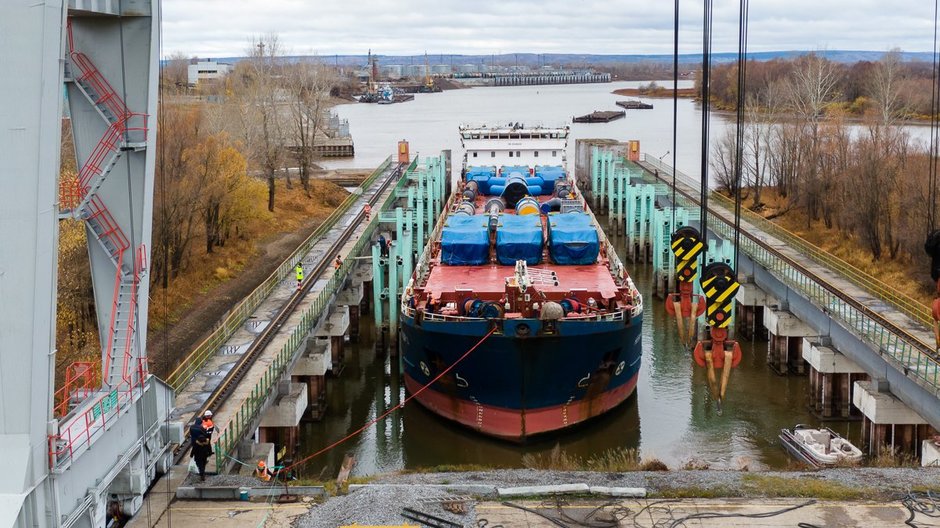
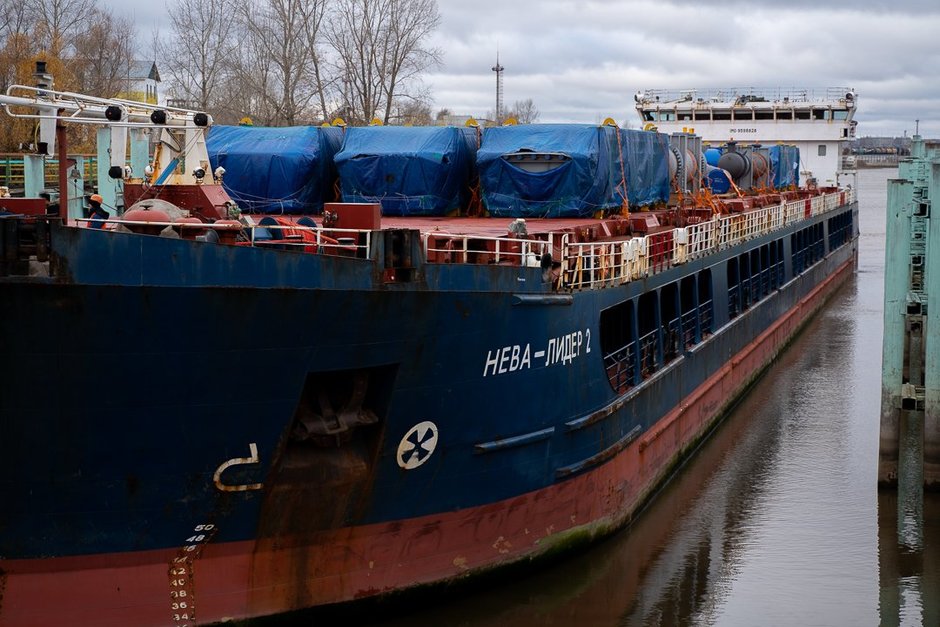
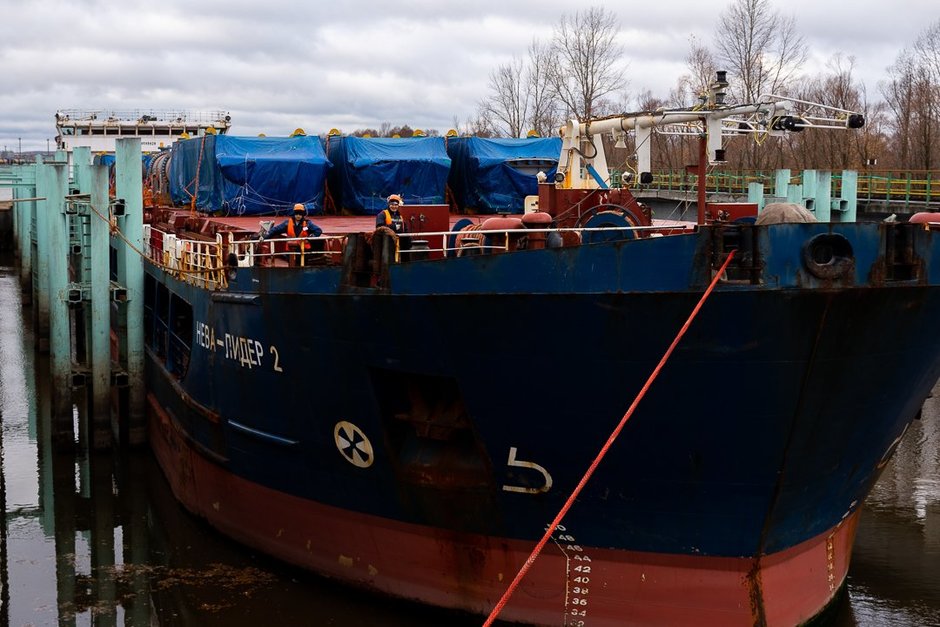
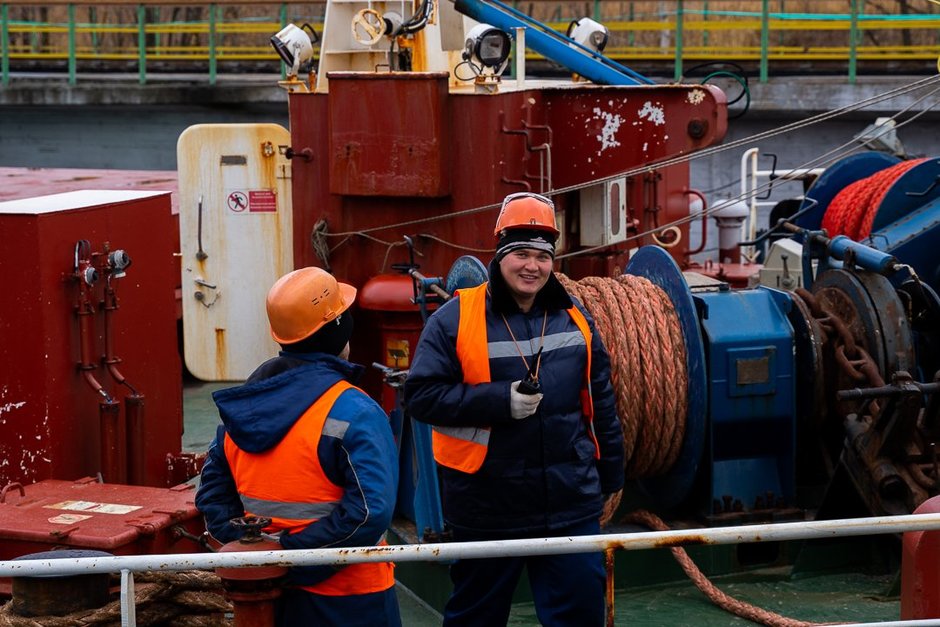
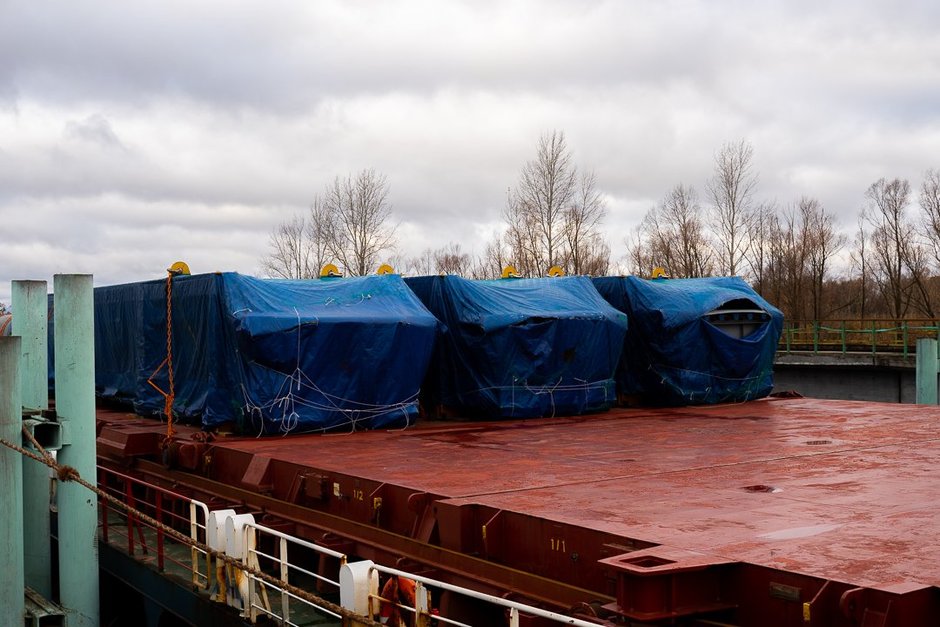
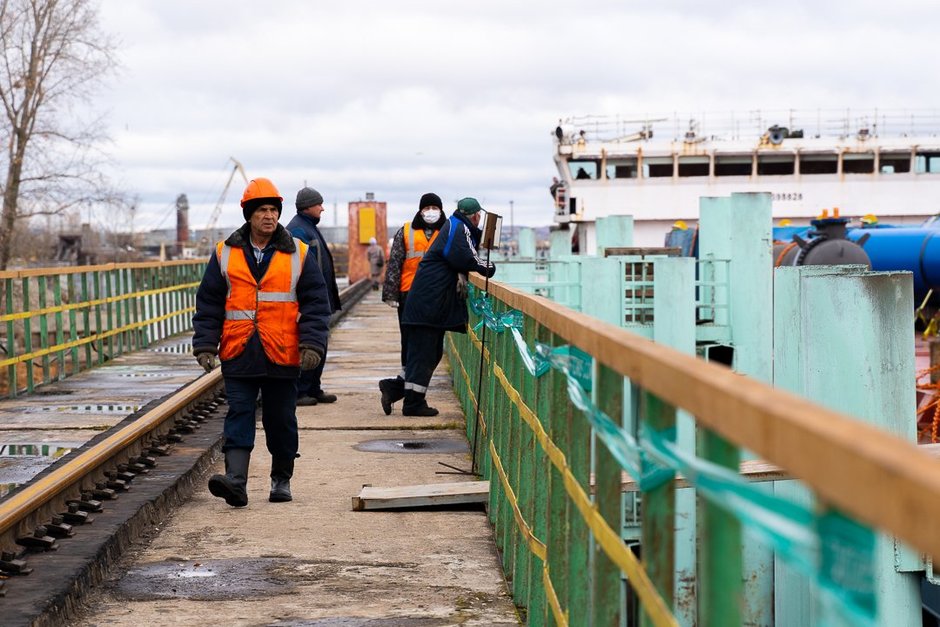
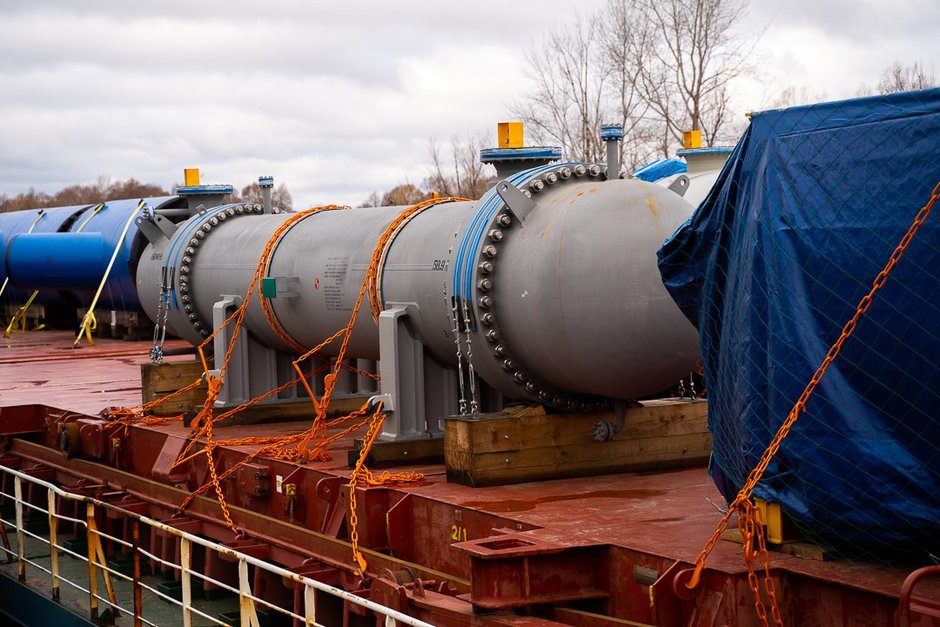
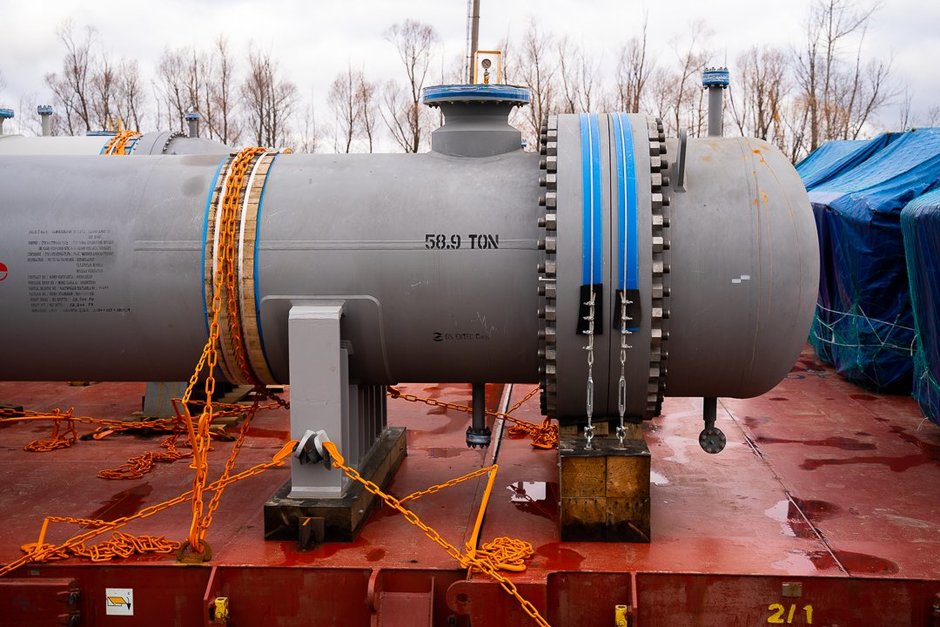
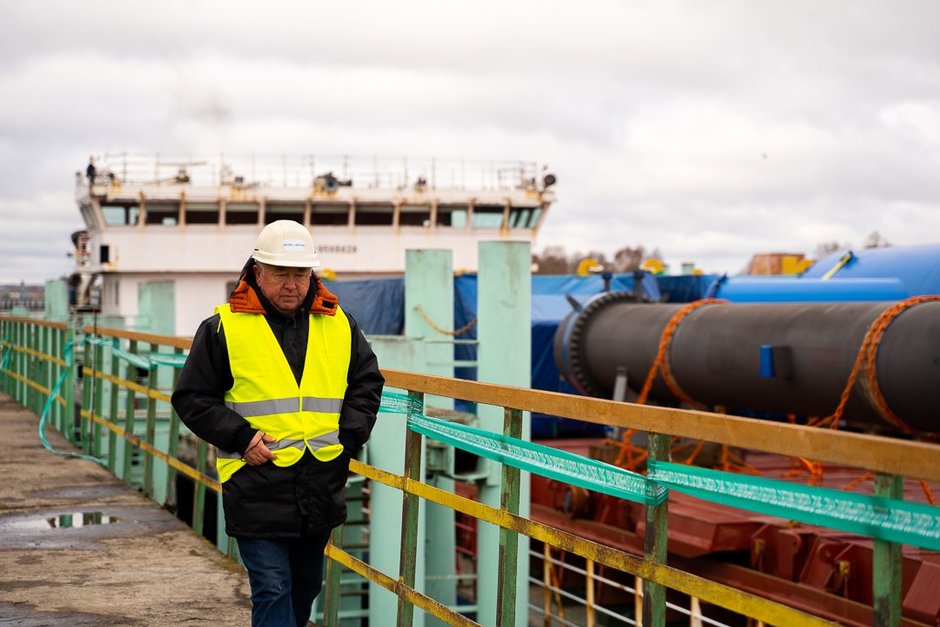
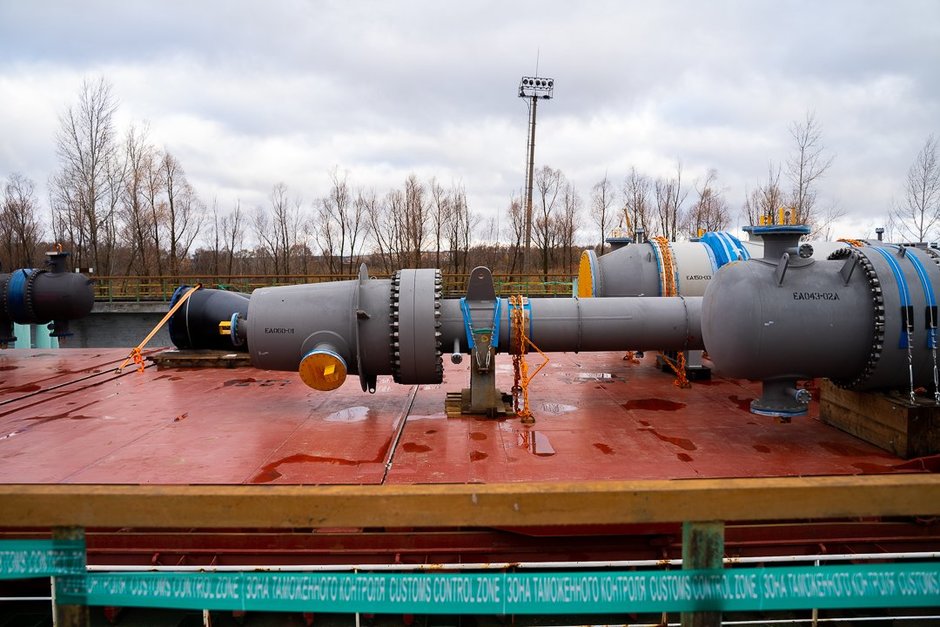
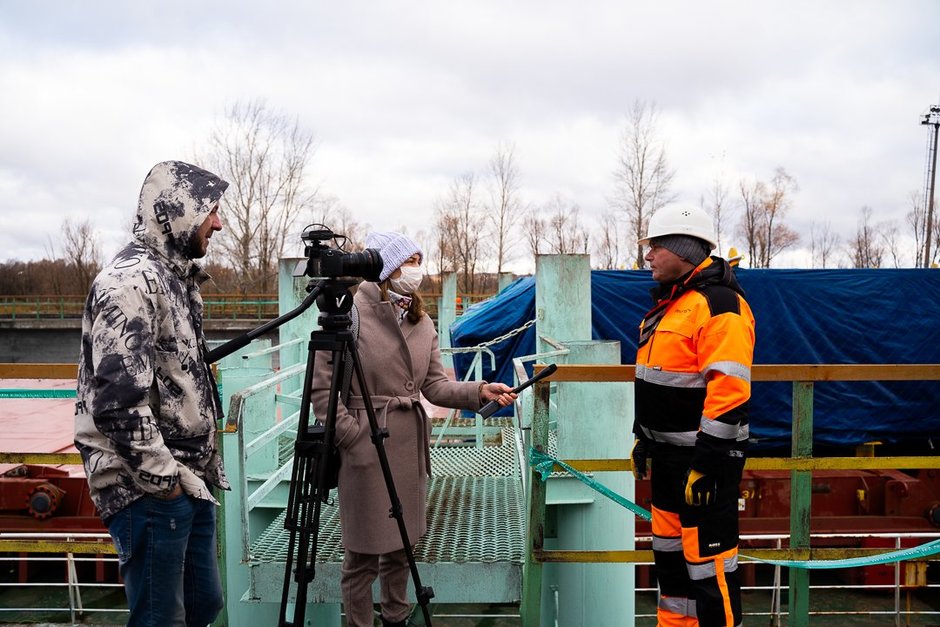
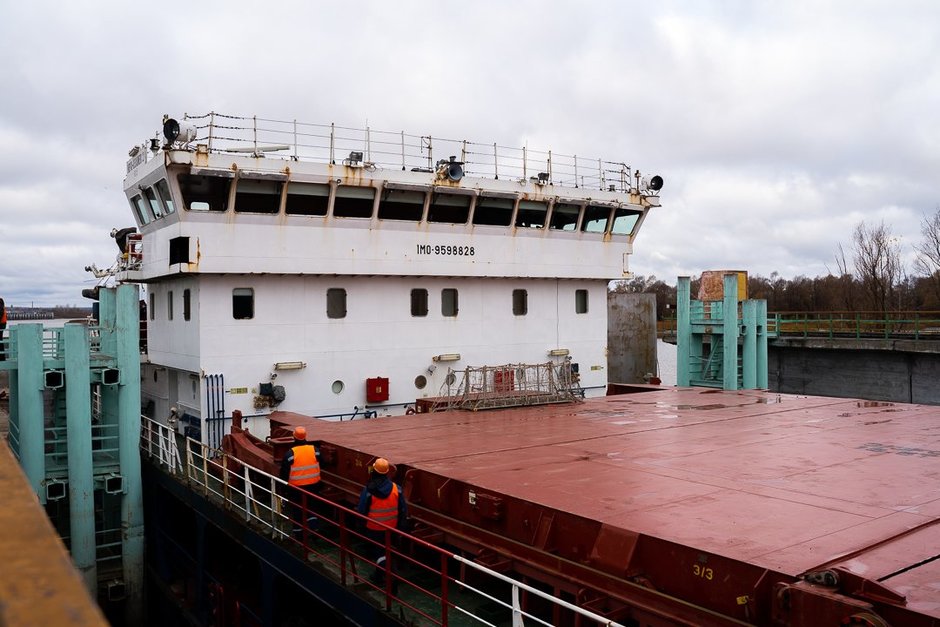
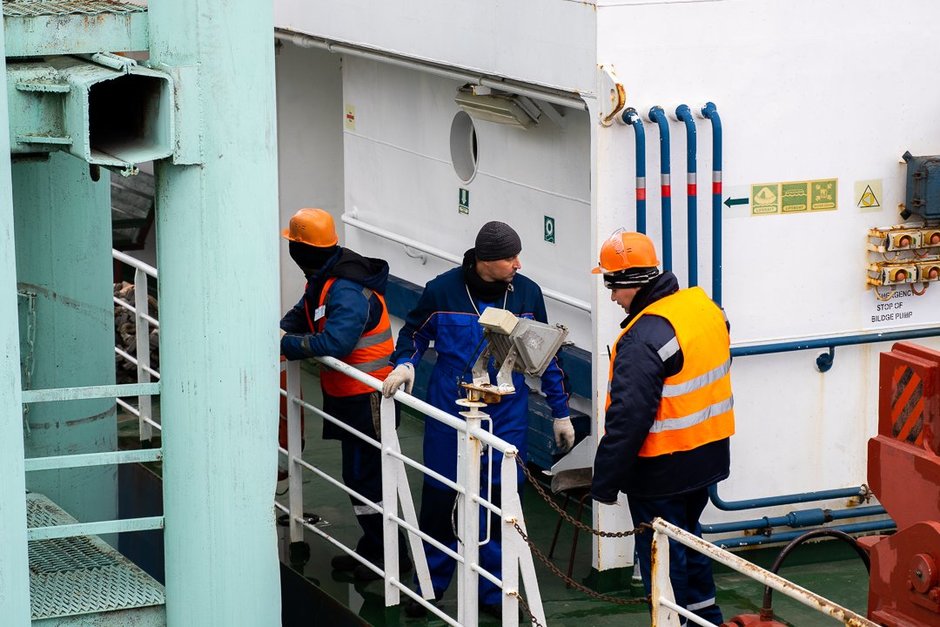
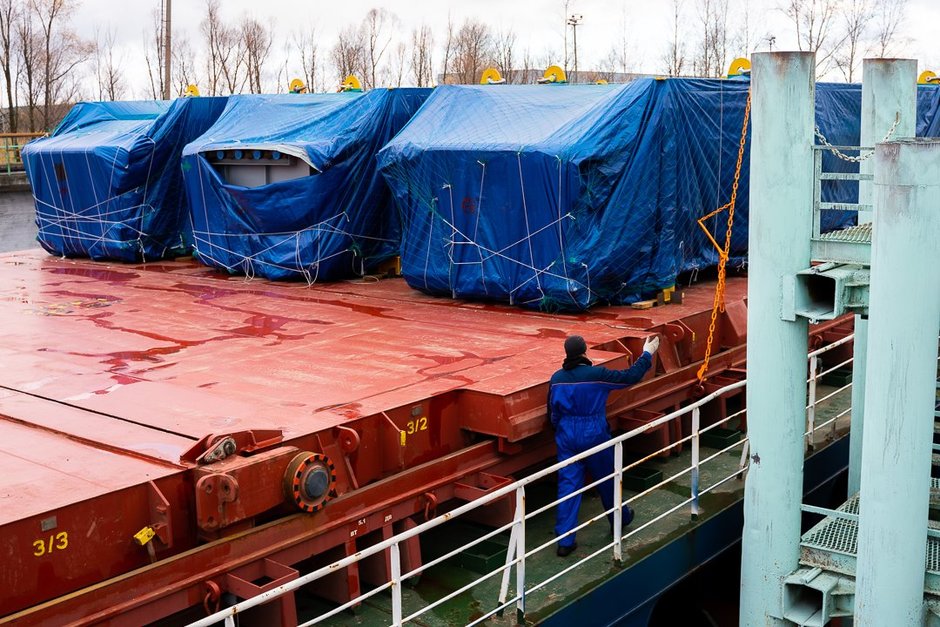
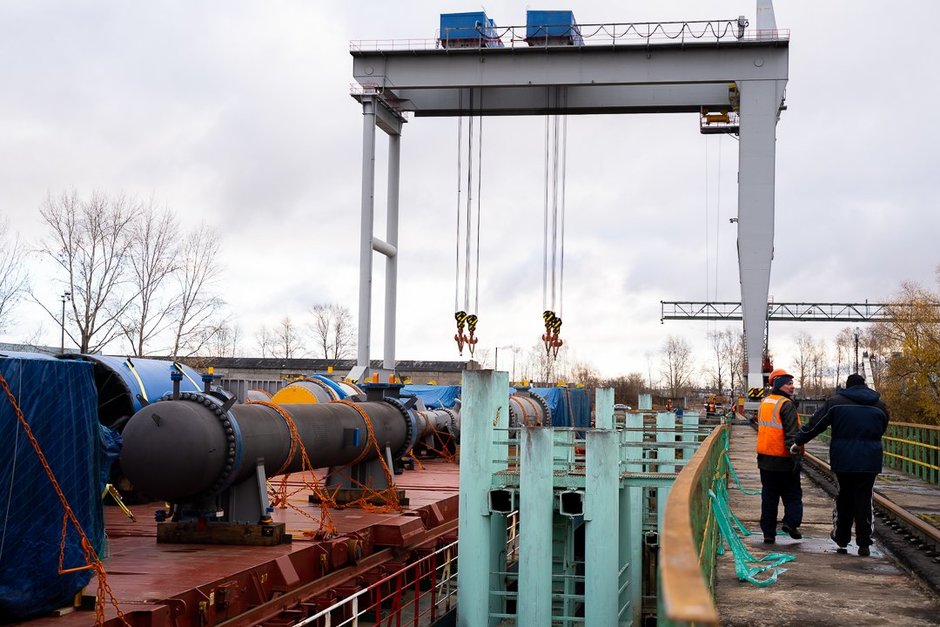
Подписывайтесь на телеграм-канал, группу «ВКонтакте» и страницу в «Одноклассниках» «Реального времени». Ежедневные видео на Rutube, «Дзене» и Youtube.