From Romania to Tatarstan: heavy equipment for NKNK’s ethylene plant arrives at Nizhnekamsk cargo port
Nizhnekamskneftekhim, which is part of TAIF Group of Companies, keeps assembling heavy equipment in the new EP-600 plant. The main construction is to end by the end of 2022, while the first product will be made six months later. Despite the coronavirus pandemic, the project’s deadline isn’t reconsidered. Nowadays pile drilling is 88% over on the construction site, the completion of cement foundation is 36%. Moreover, 80% of heavy manufacturing equipment has already been delivered to Nizhnekamsk by water. The fifth ship with heavy freight arrived in the river cargo port from Romania on 28 August.
On schedule
It’s 9 a.m. Saint Prince Vladimir arrived at the river cargo port. It has 13 pieces of the column and 15 pieces of the heat exchanger aboard. The ship moored on time. Despite difficulties caused by the coronavirus pandemic, the licensor of EP-600 project Linde is delivering equipment on schedule.
Saint Prince Vladimir has impressive dimensions. Its length is 128 metres, width is 16,5 metres, it is six-floor high. Before mooring to the Nizhnekamsk port, the ship crossed the Black and Azov Seas, the Don, Volga and Kama.
The heavy freight was loaded abroad in the Port of Constanța in Romania where it was delivered by an ocean liner from South Korea.
“It took us two weeks sharp to get here from Romania non-stop. We’ve covered over 3,100 kilometres, 27 gates. We have about a thousand tonnes of manufacturing equipment on board. We have kept to the schedule,” says Kirill Chashkov, a senior aide on Saint Prince Vladimir.
It is the fifth ship that has arrived with freight for the future ethylene plant of Nizhnekamskneftekhim PJSC this year. It is mainly a heat exchanger for different units in the plant: DA022-01 spent caustic steam stripping column, С3 DA024-01 fraction absorber, С2 DA026-01 fraction absorber, С3 DA035-01 fraction steam stripping column, DA037-01 petrol stabiliser and others.
“About 150 pieces of equipment for the construction of the EP-600 have been delivered in total. Another two ships are expected in October. We’ve managed to deliver 80% of the main heavy equipment during this navigation period. We plan to finish the transportation by the end of October. If the delivery of equipment is anyway postponed until next year, the amount will be insignificant,” says Sergey Rutman, a manager of Deugro Project.
264 pieces of equipment will be delivered by water in total, 17 of which are heavy.
“The logistics of equipment delivery is complex enough. The ocean passage from Korea where most its part is made to Romania takes about 30 days. In Constanța, the freight is transferred into a ship or barge that spent about 14 days to get to Nizhnekamsk. In the end, the delivery takes almost two months. Difficulties arose because of the pandemic, restrictions on people’s mobility were imposed. We looked for solutions. We sent our employees to Nizhnekamsk and Romania. Now the situation has simplified,” notes Sergey Rutman.
Upon arrival at the port, the equipment is unloaded to the riverbank and transferred into tractor units with the help of special cranes. Roads were expanded, obstacles were removed, temporary structures were built to deliver the columns to the construction site. The equipment is partly sent from here to interim warehouses (the equipment base of Nizhnekamskneftekhim PJSC) and directly to the construction site for assembly.
Deployment of 980 people and 135 pieces of machinery
The assembly of the heavy equipment on Ethylene-600 olefin facility, which is under construction, began on 22 June 2020. On this day, the first and heaviest primary fractionating column that is 640 tonnes in weight, 8 metres in diameter, 78 metres high was installed on the site of the future plant. The equipment is designed to remove heavy hydroсarbons and coke from pyrogas. Nizhnekamskneftekhim Director General Ayrat Safin witnessed the milestone. He noted the importance of the new plant for the development of the economy not only in the enterprise but also in the whole region.
“The ethylene facility is a continuation of the development of our enterprise, increase of production of commodities, payments to the republican budget,” said Ayrat Safin. “This project is economically and socially profitable for the whole republic and Russia in general from all angles. Nizhnekamskneftekhim’s economic performance will go up, this is will influence a rise in the well-being of our workers and Nizhnekamsk citizens, which, in turn, will become a stimulus for further development of the city, the region and the country.”
13 columns have already been installed on the EP-600 construction site at the moment. Metal structures are erected at the same time. 980 people and 135 pieces of machinery are deployed. Over 260,000 cubic metres of foundation pits have been dug, more than 24,000 piles have been drilled, over 33,000 cubic metres of the foundation has been laid. The improvement of the construction town began on the site, underground networks have started to be laid.
Nizhnekamskneftekhim PJSC Director General Ayrat Safin personally controls the course of construction works in the new EP-600 plant. He recently visited the production site of the construction project’s main contractor Gemont company where pipe spools are manufactured for the new olefin facility. Specialists talked about every stage of production and strict quality control. According to them, the pipe spools are sent to the construction site for further assembly only after a thorough examination.
Automation of supplies and equipment delivery
The organisation of control over the delivery of equipment and materials, provision of communication, quick and accurate information are another important condition of the implementation of the project. For this purpose, specialists of Logistics Business Process Automation Office of Nizhnekamskneftekhim’s IT Department launched automated processing of machine-readable files of packing lists, invoices and bills received from suppliers of the equipment and materials in every shipping.
Information from machine-readable files is used to create documents, which are necessary for the reception in the warehouse, in the enterprise’s management system SAP ERP. Before placing an order for delivery, the system automatically searches for the code of a material and equipment in the reference book and creates a new unique note with a code if needed.
The materials and equipment are classified according to the received amount of information in packing lists, invoices and bills, features that influence the further life cycle of materials and in the end accuracy in accounting records at the stage of construction and after the facility is put into operation are filled in.
Specialists can also quickly track a parcel, give the contractor materials and equipment, control the amount of works done.
Local treatment plants and smokeless flares
Nizhnekamskneftekhim plans to complete the main stage of construction of EP-600 in December 2022 and launch the first product in late 2023. The new ethylene plant will allow annually producing 600,000 tonnes of ethylene as well as 272,000 tonnes of propylene, 246,000 — benzene, 88,000 — butadiene.
Nizhnekamskneftekhim’s new ethylene plant will be built with the use of the latest technology. The facility won’t have a negative environmental impact — positive reports of a state environmental and the main state inspection confirm it. Its own local treatment plants will allow reducing consumption of the Kama River’s resources: industrial water will be treated and reused in the plant. The flare won’t have smoke: released hydrocarbon will be burnt, and only carbon dioxide will end up in the atmosphere. Nizhnekamskneftekhim implements the project together with Germany’s Linde concern, a basic agreement with which was signed in Saint Petersburg in June 2017. Gemont company from Turkey became the main contractor of construction and assembly works.
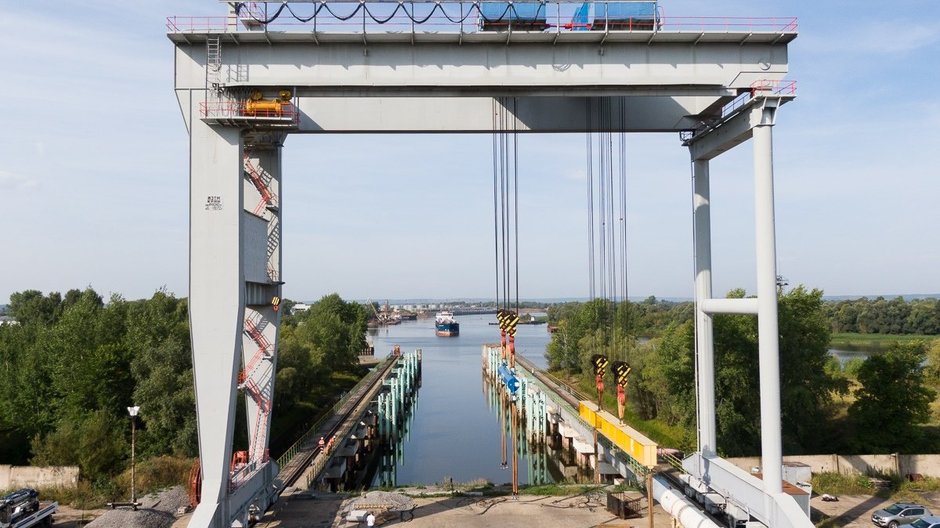
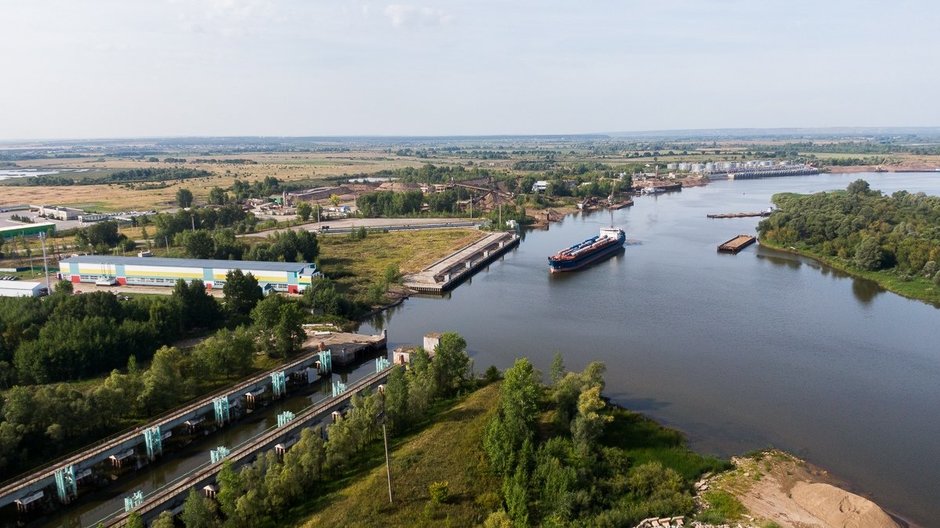
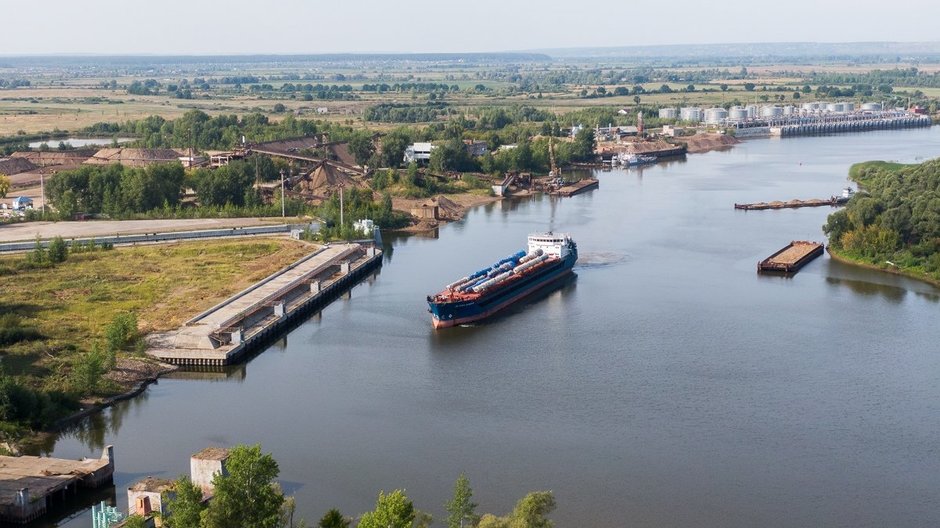
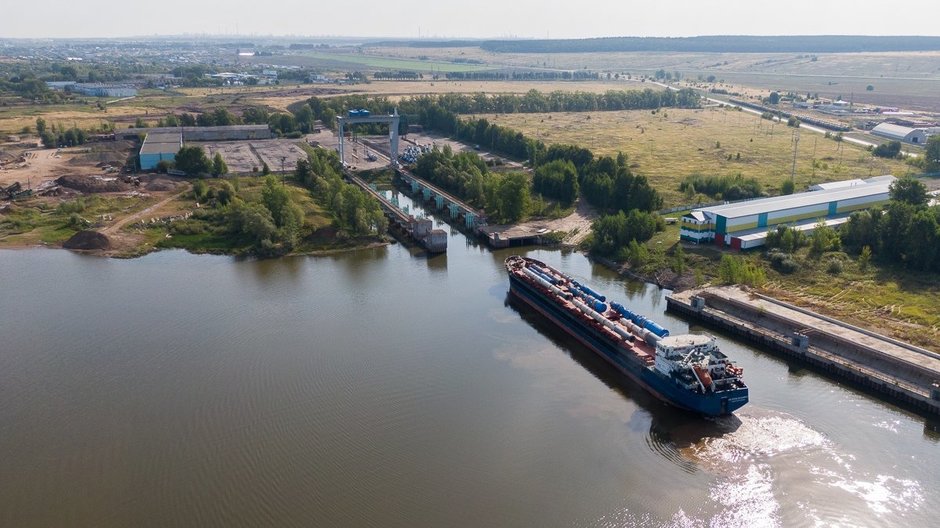
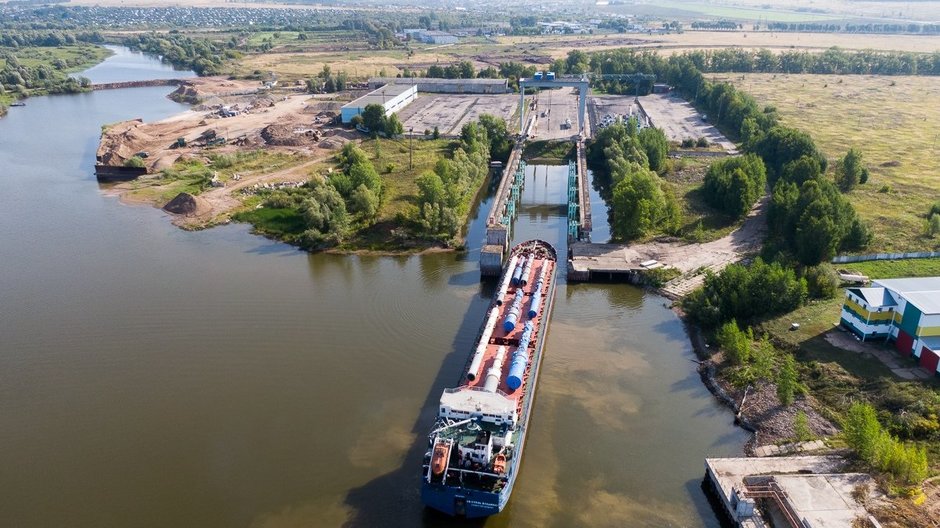
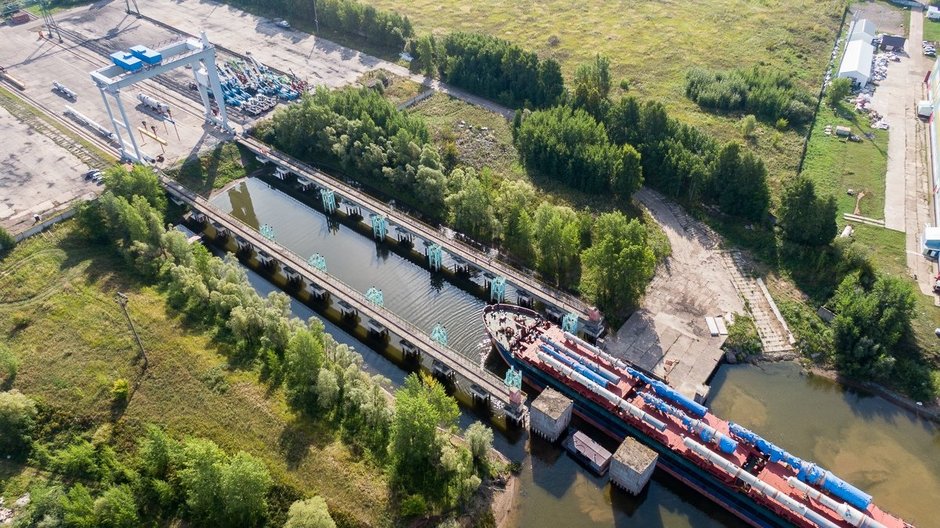
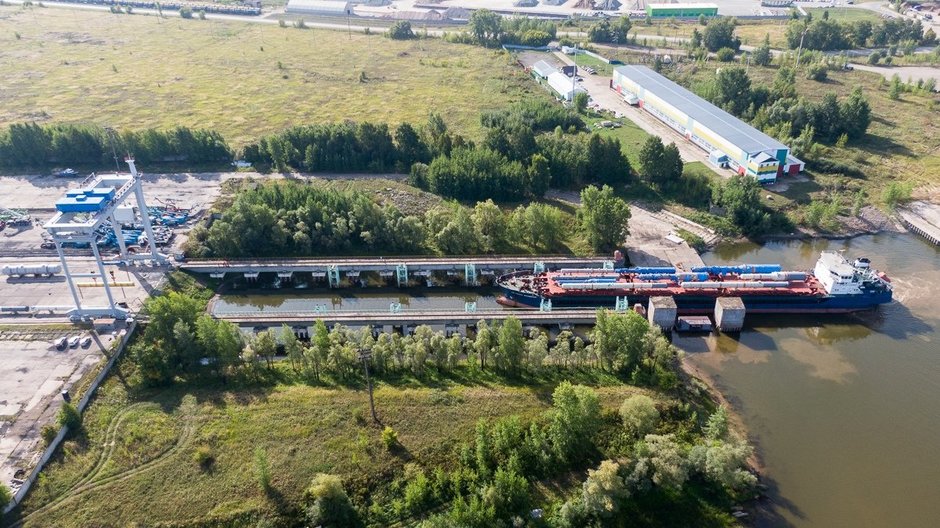
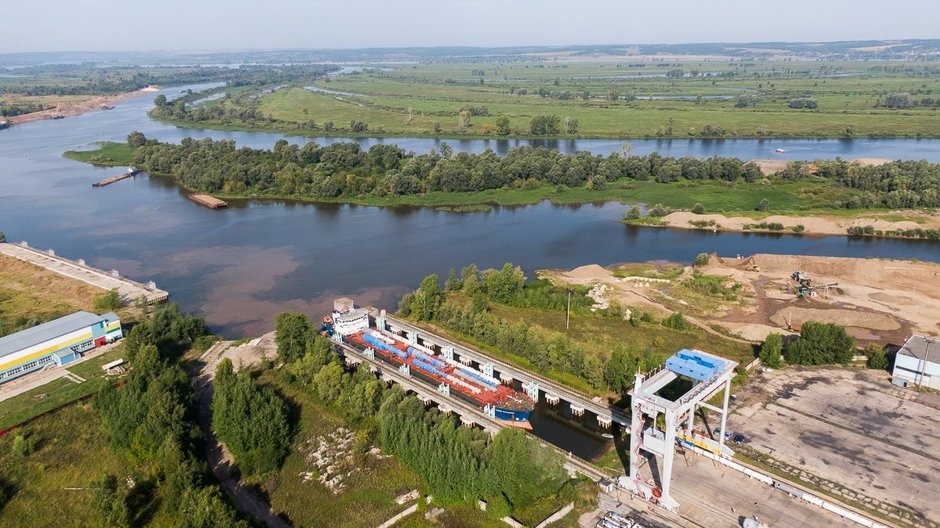
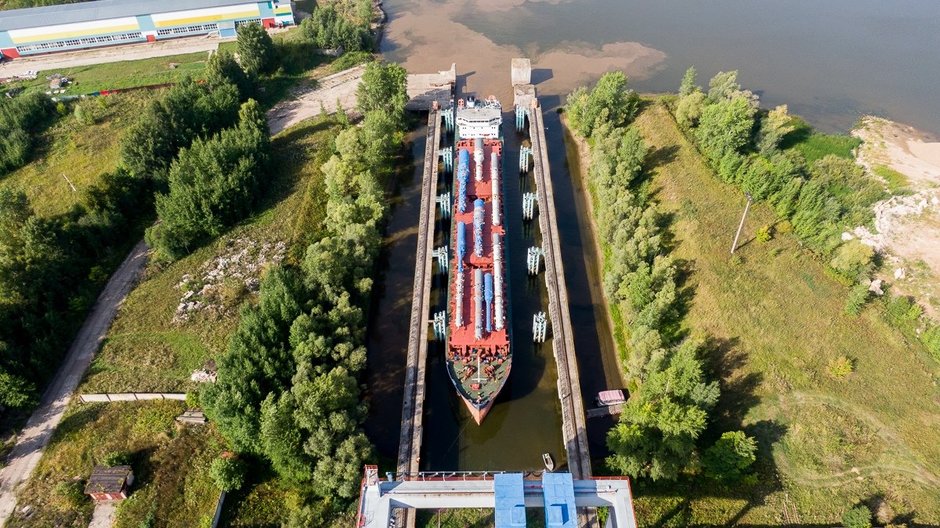
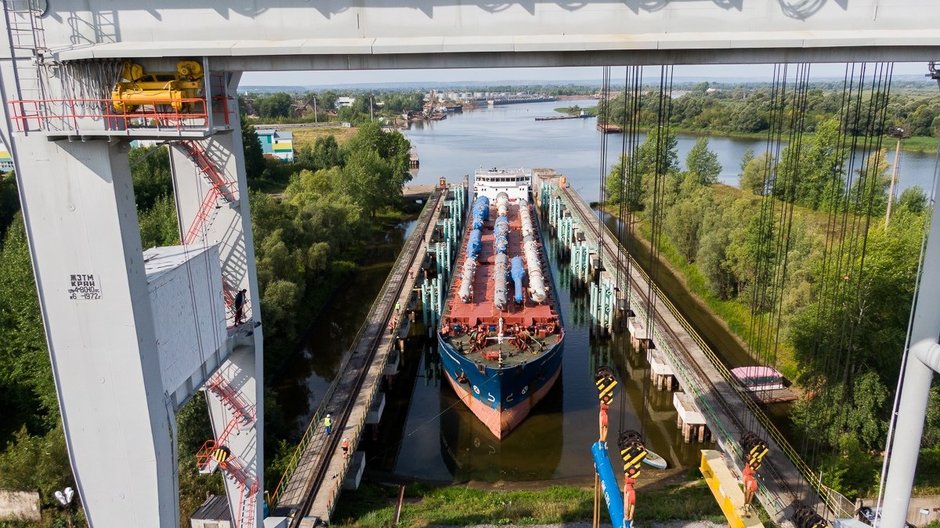
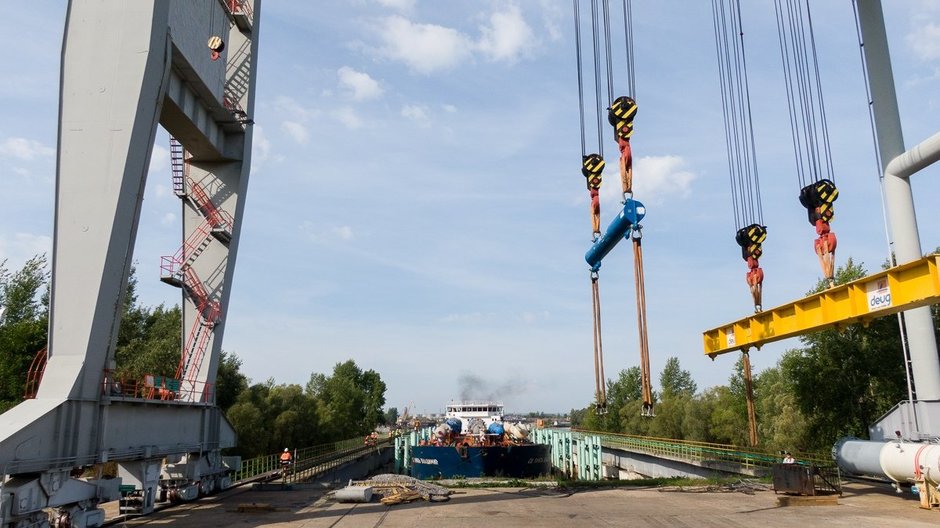
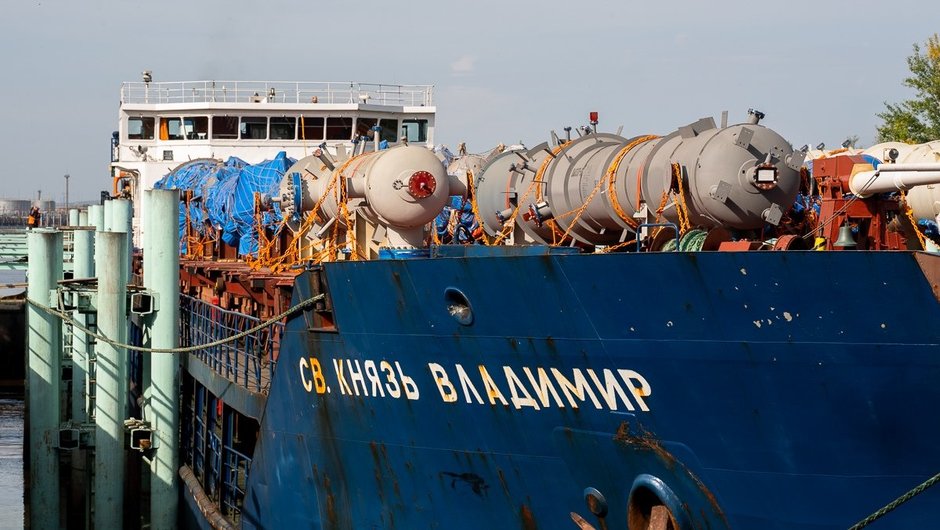
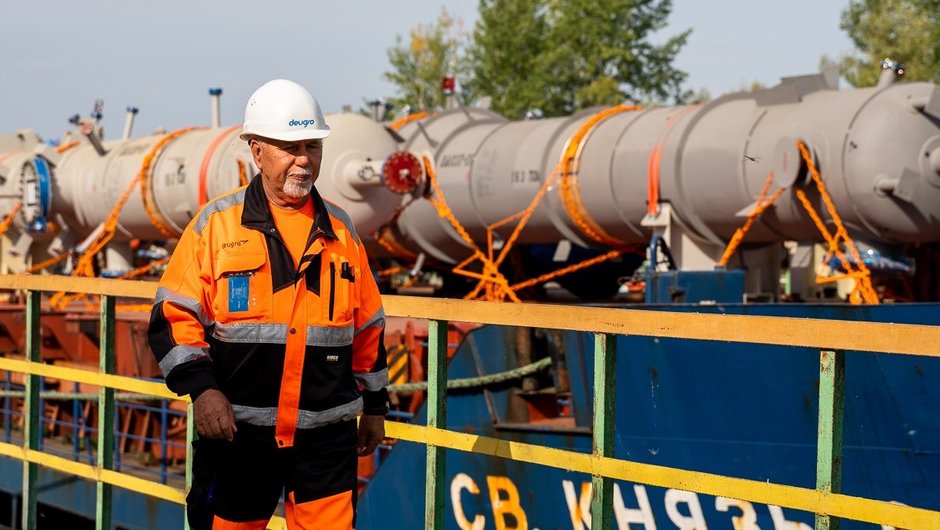
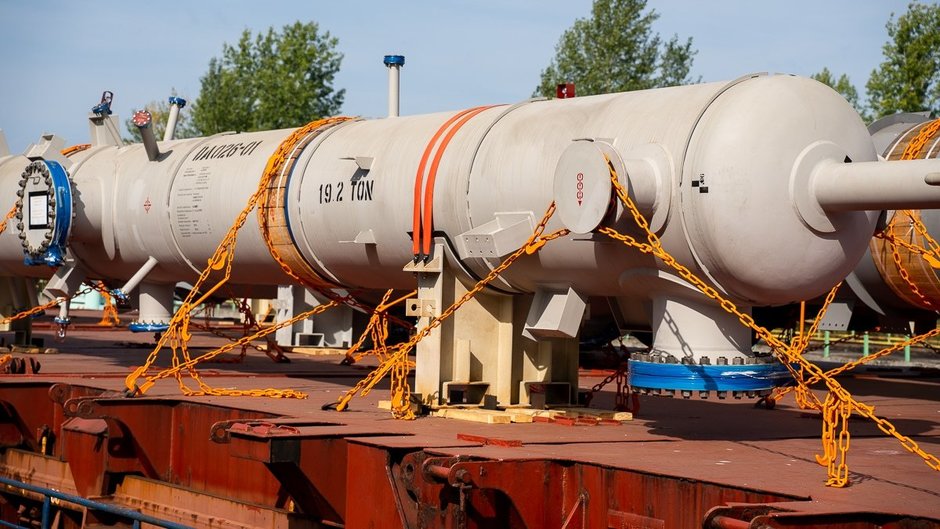
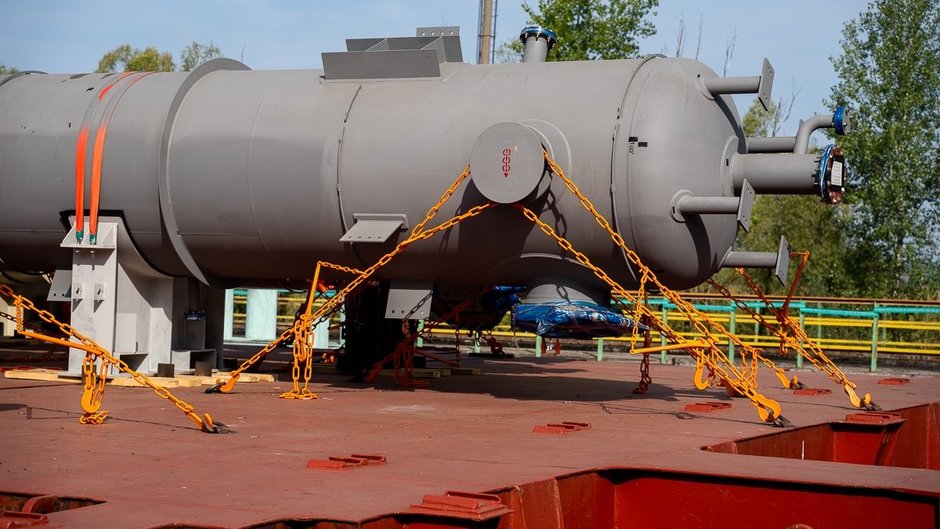
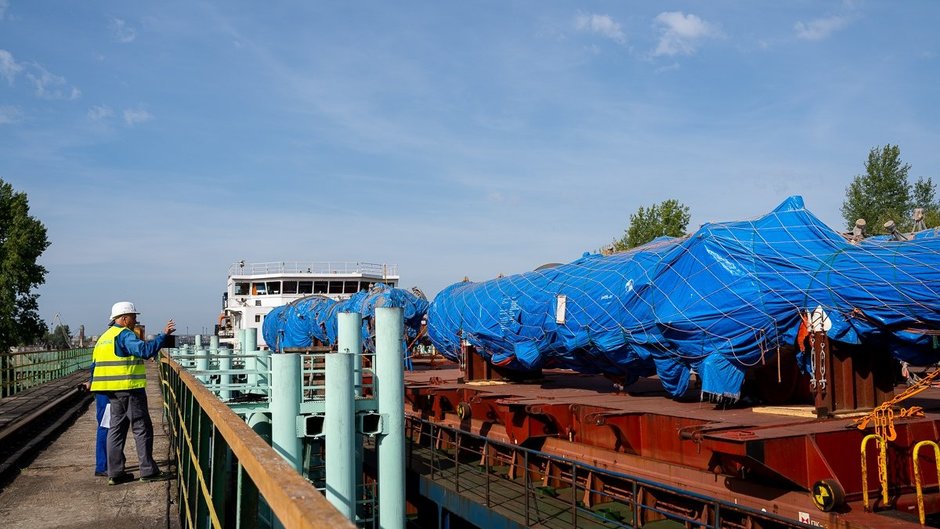
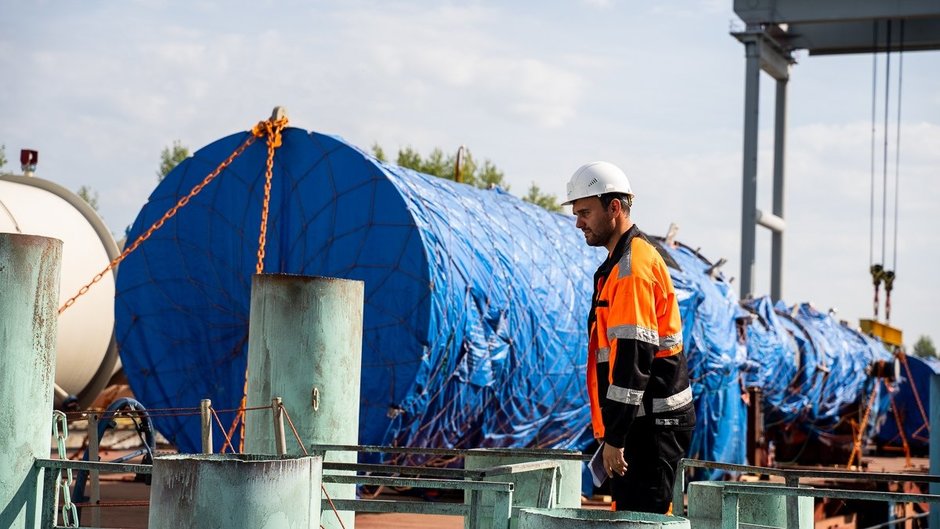
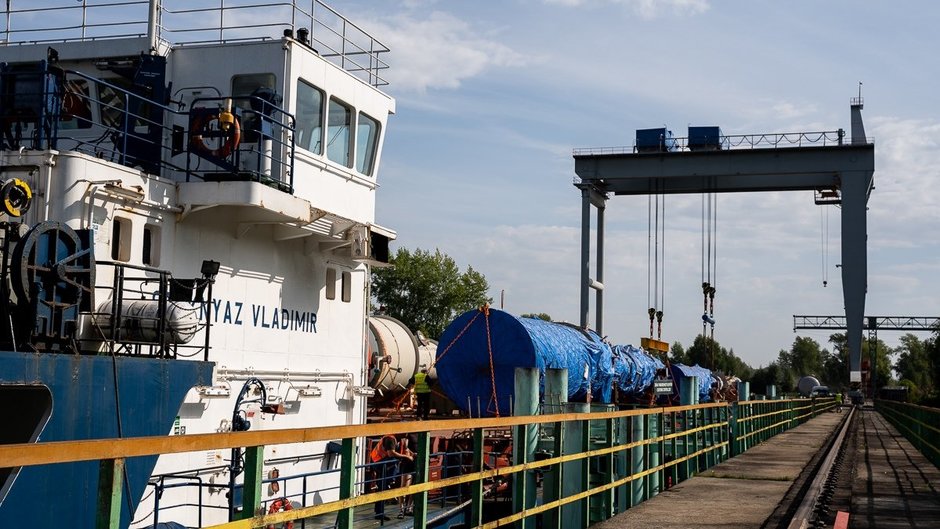
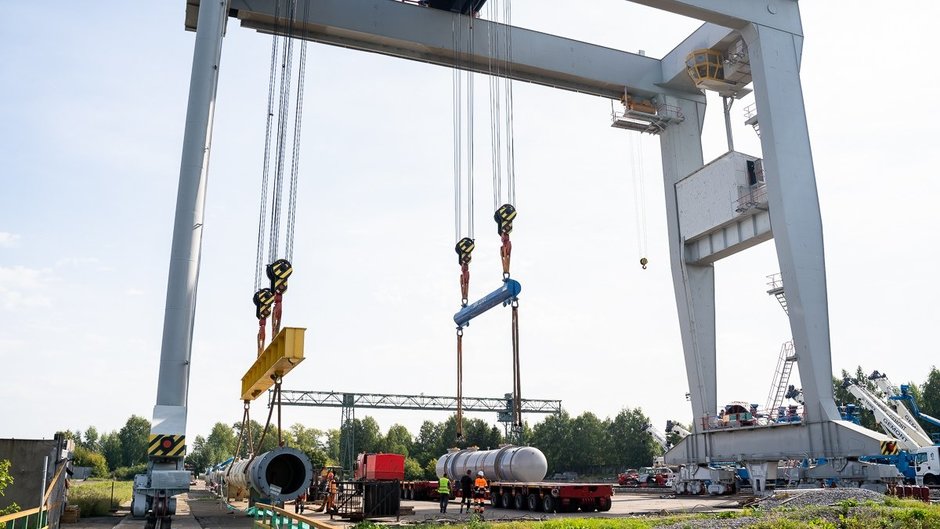
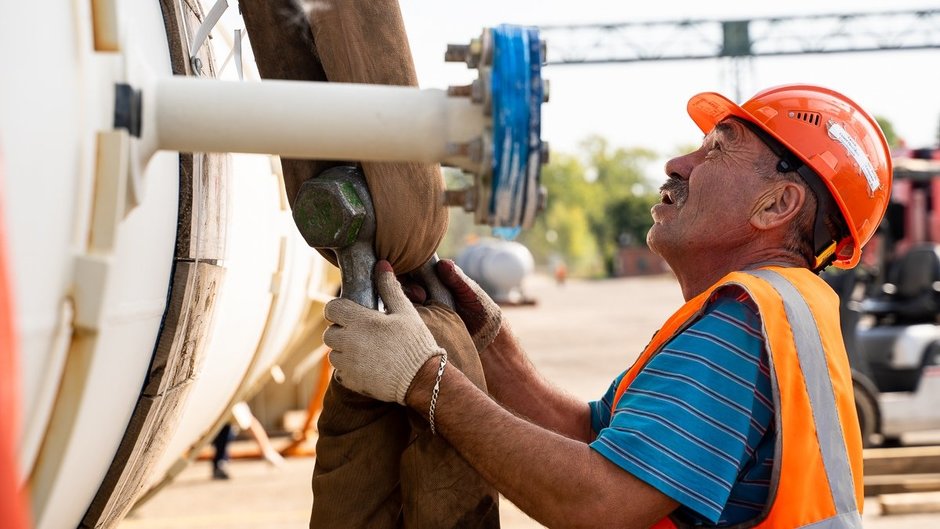
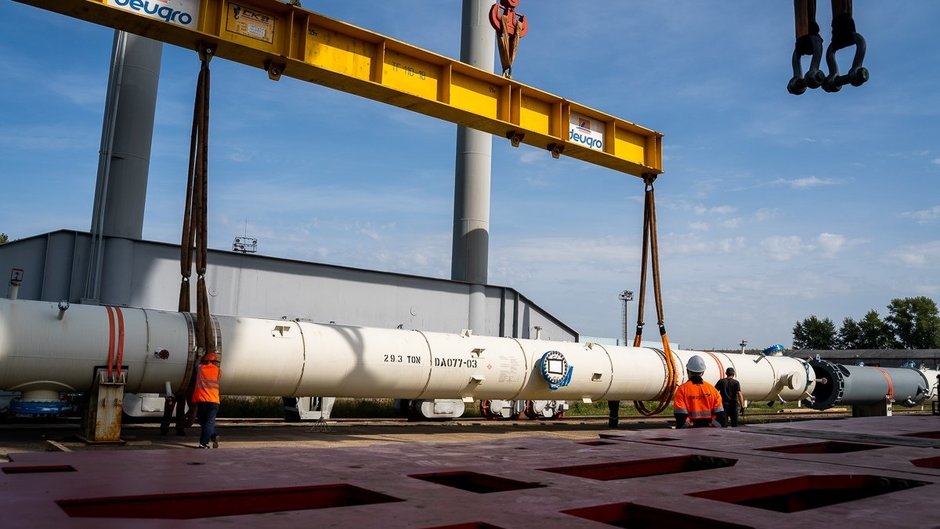
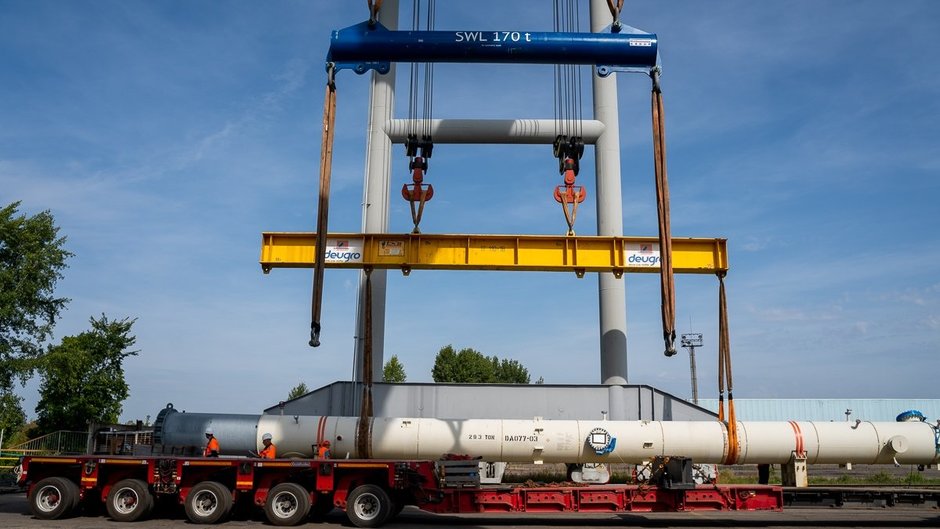
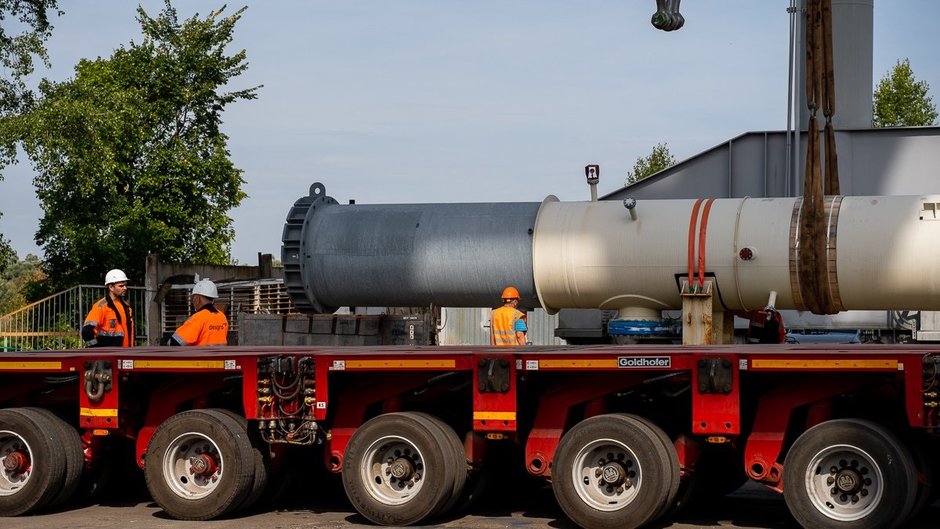

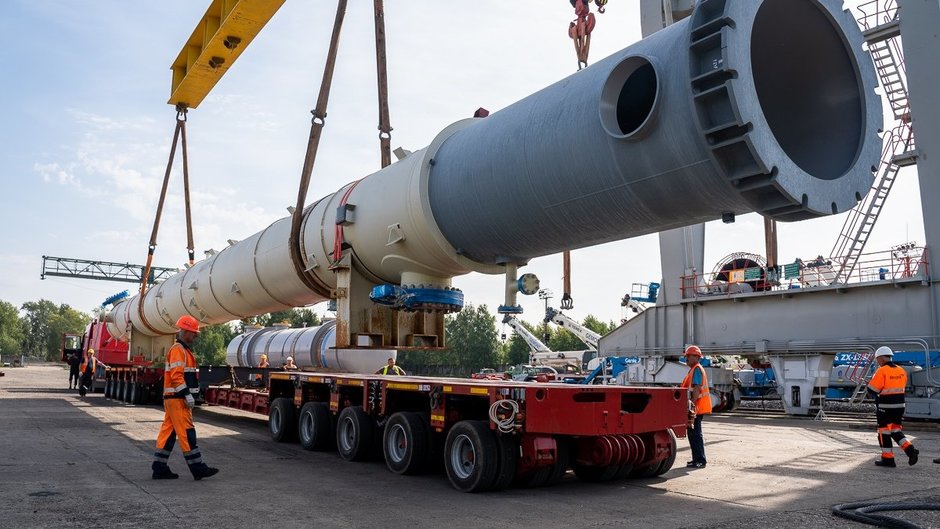
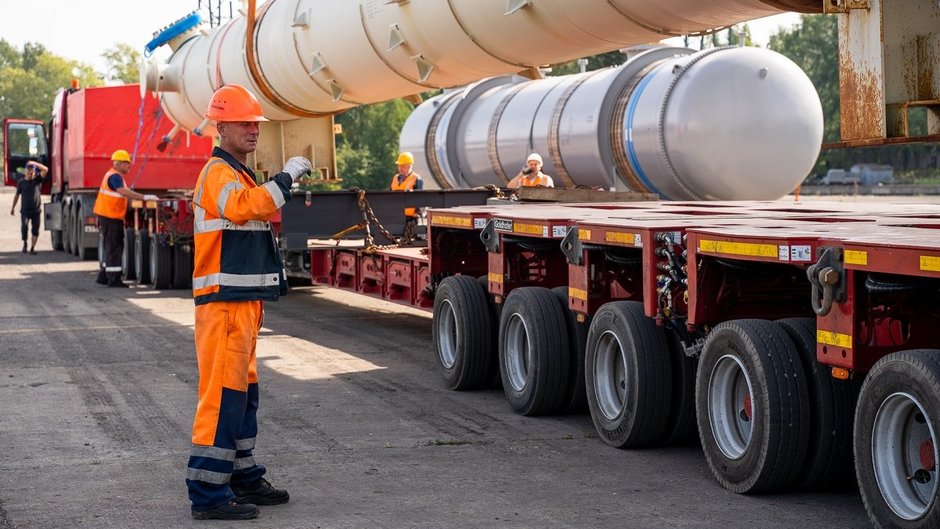

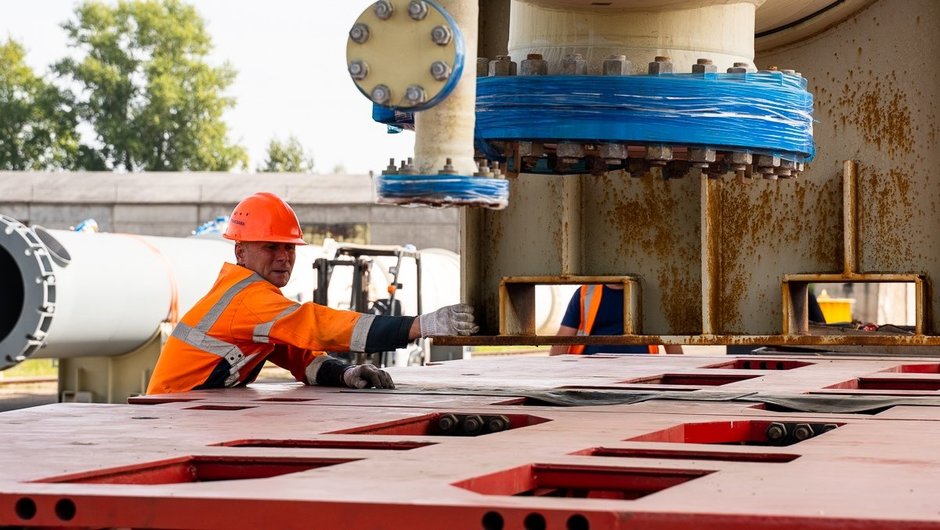
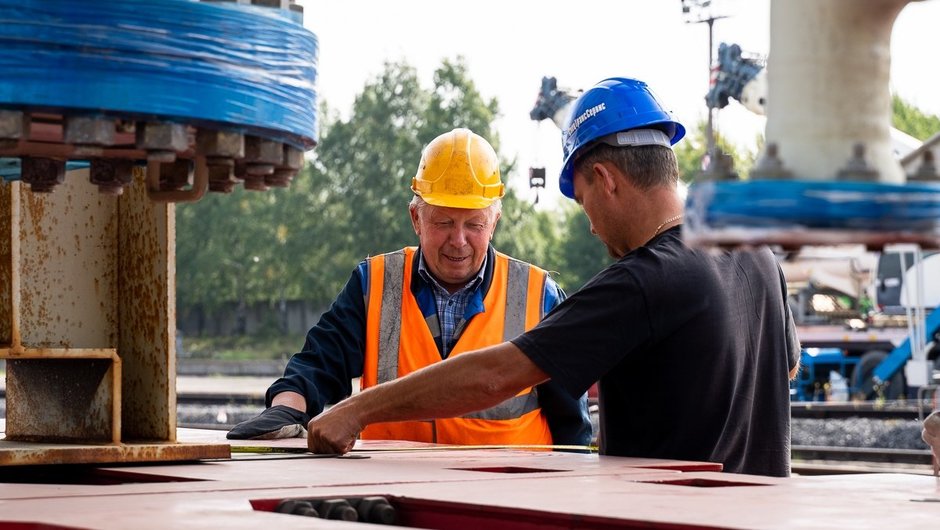
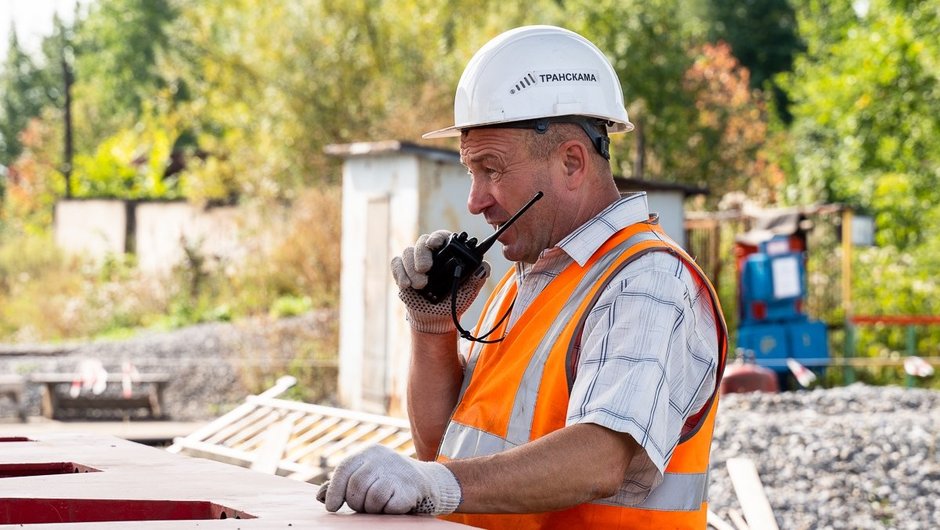
Подписывайтесь на телеграм-канал, группу «ВКонтакте» и страницу в «Одноклассниках» «Реального времени». Ежедневные видео на Rutube, «Дзене» и Youtube.