HRCC: raw materials — worse, products — cleaner
VCC technology makes it possible to obtain oil products of the highest quality from heavy oil distillation residues
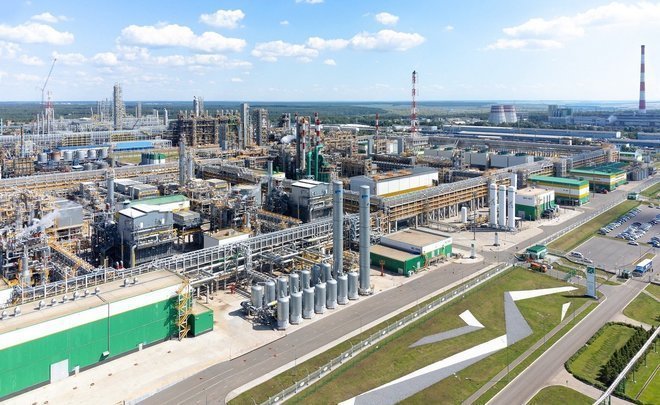
Truly high convertion of crude oil is the maximum extraction of high-quality oil products from raw materials, even not of the best quality. And it is possible, which is proved by the team of the Heavy Residue Convertion Complex of TAIF-NK JSC. How such products differ from those obtained using technologies that have already become classics of processing, and what else are they preparing to offer the Russian and global industries in Nizhnekamsk — read in the material of Realnoe Vremya.
There will be more and more such units in the world
On November 3, 2021, permission was received to put into operation a production that could safely be called unique for the oil refining industry of the world. VCC or Veba Combi Cracking is a technology known since the beginning of the last century. In 1913, German scientist Friedrich Bergius proposed the technology of catalytic hydrogenation of coal when exposed to hydrogen under high pressure and at high temperature. In the 1940s, attempts were made in Germany to introduce it. After the Second World War, against the background of the presence of light oil on the markets and low oil prices, the patent was forgotten on the shelf for many years. Only at the border of the 20th and the 21st centuries they decided on resuscitating it. In China, two units were built in a classic solution for the technology, with an emphasis on coal as a raw material, and in Tatarstan they followed the path of implementing a larger project, where heavy oil distillation residues — tar are used as raw materials.
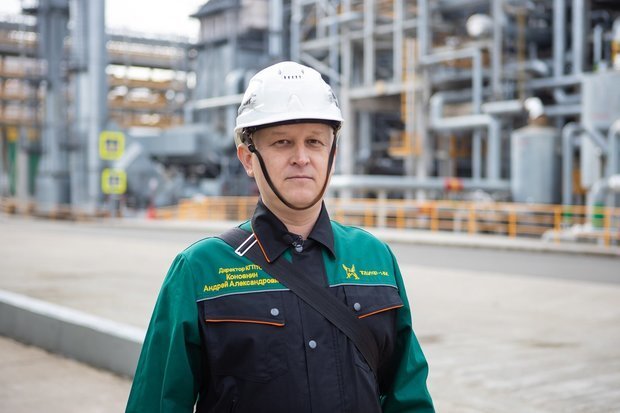
“The main difference between VCC and standard cracking is the presence of separate reactor units operating with a suspended layer of coal additive: this helps to remove heavy metals, which are catalytic poisons, from the tar. The additive adsorbs all metals and those substances that can spoil the final product," the director of the HRCC, Andrey Konovnin, told the journalist of Realnoe Vremya.
Today we can confidently say that the technology implemented by TAIF-NK does not just work. After being refined by Russian, Tatarstan, and TAIF specialists, it became the best — the most efficient in the global oil refining industry.
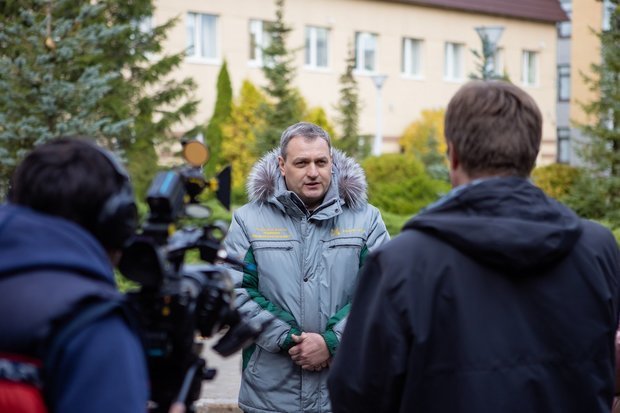
“For Tatarstan, the commissioning of the HRCC gave at least an increase in deductions to both the consolidated budget of the Republic of Tatarstan and the budget of the Russian Federation. For Russian and world oil refining, it is an image that a republic like Tatarstan was able to implement such an arch-complex project, bring it to mind, and today it is working. I am sure that everything is still ahead, and there will be more and more such units in the world over time. Because this is a truly deep oil refining, if we talk about it frankly," said Maksim Novikov, the director general of TAIF-NK JSC.
A low-margin “by-product” — into a quality product
Tar is what used to remain after the extraction of high-quality light oil products from oil with the help of affordable TAIF-NK production facilities. Certainly, there is always a buyer for tar, but it costs much less than the same oil from which it is obtained. For production, this is a loss. Loss of time, effort, money. The commissioning of the Heavy Residue Convertion Complex into pilot operation has radically changed the situation.
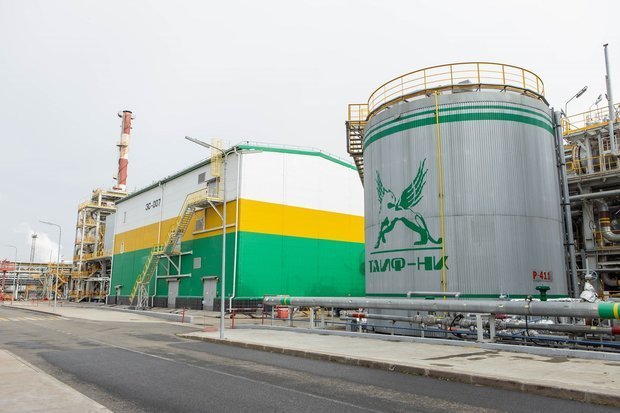
“We must understand that the process of obtaining products from tar is completely different. This is not just a physical process of separating oil into fractions and refining these components. Here the work is going on at the molecular level: crushing heavy molecules into lighter ones — the same naphtha, diesel fuel, etc. Yes, of course, there are differences in the hydrocarbon composition, they cannot be. But this does not affect the performance characteristics of the final product in any way, and users of TAIF-NK products will not find any difference for themselves. Unless they note that the quality has become even higher," Maksim Novikov said.
It was the raw materials that Aleksey Khramov, the chief engineer of TAIF-NK JSC, began to talk about in the first place, answering a question from the journalist of Realnoe Vremya.
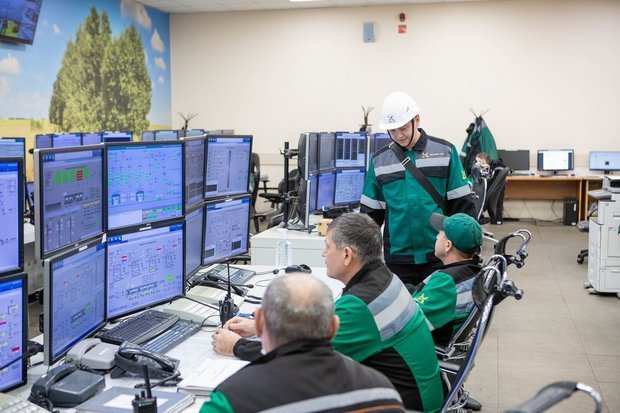
“Obviously worse raw materials are processed at the Complex. If crude oil or vacuum gas oil is supplied to the primary processing or catalytic cracking plants, then by and large the “waste” of vacuum distillation of oil is delivered to the HRCC. Despite the low quality of raw materials, HRCC products turn out better, cleaner. All products obtained here, with the exception of the residual product in a small amount, contain sulphur below 10 ppm. These are deeply desulphurised products. Nafta, which goes to the subsequent stages of redevelopment, also has a slightly modified group composition. And, which is very convenient for technologists of subsequent conversion, this composition can be adjusted. Jet fuel of the HRCC, has unique indicators for the crystallisation temperature: much lower — 60° C. The indicators for the height of the non-smoking flame are unique, the operational properties are higher. HRCC winter diesel fuel has significantly lower indicators of low-temperature properties and can be used as a component to Arctic winter diesel fuel. HRCC summer fuel has high cetane numbers and the best high-temperature properties. Well, as a nice bonus, in all fuels produced by the HRCC, sulphur is less than 5 ppm, and this is a multiple lower than the GOST requirement," Aleksey Khramov emphasised.
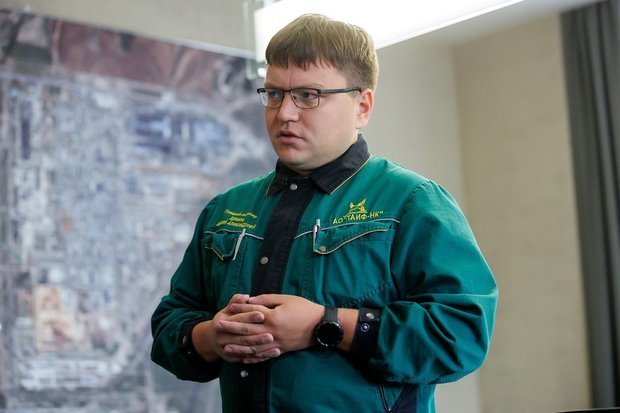
“We have already separately developed documentation on Arctic fuel, now we are working on the flexibility of production of winter diesel fuel, jet fuel — at the same time. The HRCC gives us the opportunity to maintain a constantly wide basket of manufactured petroleum products. And we have something else to think about. One of the big projects right now is in the works — it concerns the residual product of hydrocracking. The result is there — that's all I can say so far. It's too early to say more," the director general of TAIF-NK JSC added intrigues.
But as such, the new production does not leave any waste. The general director of the company, Maksim Novikov, focused on this.
All processes are under strict control
The laboratory of the Heavy Residue Convertion Complex was formed almost simultaneously with the beginning of the construction of the HRCC itself. In 2016, it was officially put into operation. And her current boss, Elena Demidova, has been working at the Complex since 2013.
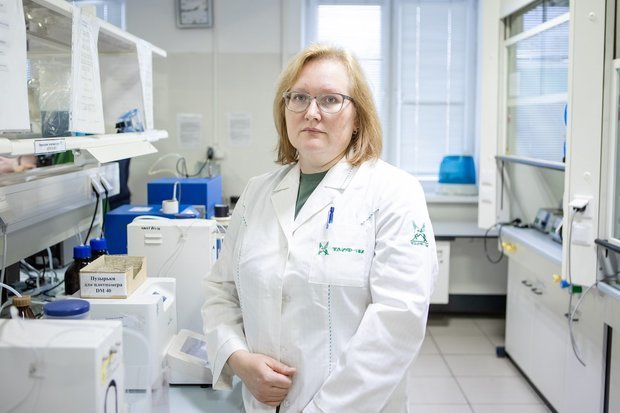
“When I came here as deputy head of the laboratory, it was a modular building in a field, and here there was only the foundation," she recalls. And she continues: “The equipment of the laboratory was carried out in the period 2013-2016. The equipment upgrade continues today. The management has supported us very seriously and still do. You probably noticed that the laboratory is equipped with high-quality modern and very technological equipment. For example, last year, a device was delivered that determines the group composition of heavy petroleum products.
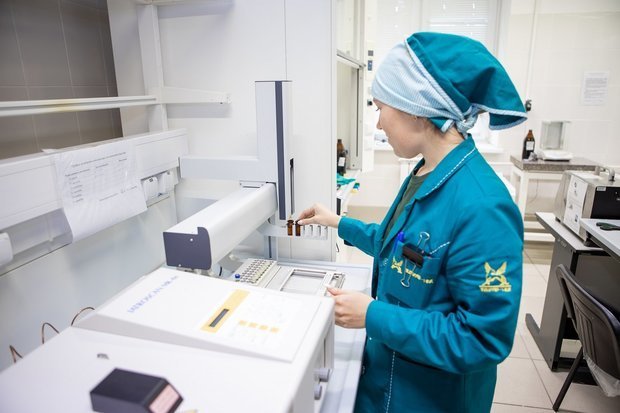
Only within one month, more than 7 thousand samples are received by the HRCC laboratory, more than 20 thousand tests and analyses are carried out. Everything is investigated: raw materials, petroleum products, steam, gas, water, amine solutions, etc.
“The HRCC laboratory is an indicator of our technological process. Any changes in technology are reflected in the results and the quality of the final product. That is why it is so important to control the technological process at all its stages. Any change in the quality of products is momentarily analysed by the operators of the technological process, as well as the analysis of these data of the plant's ITR with subsequent prompt decision-making on the correction of the technological regime," explained Ramzil Minigulov, the head of the Technical Department of the HRCC.
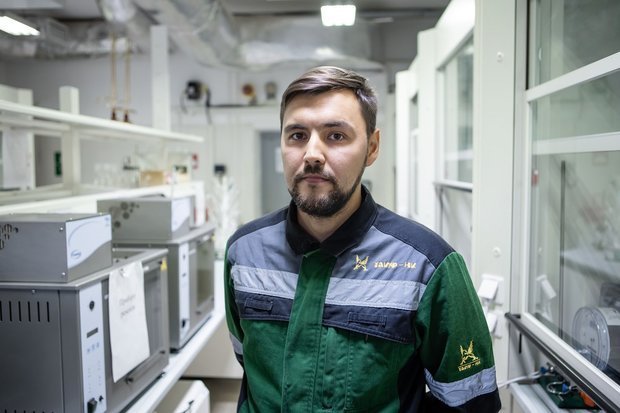
Sampling at all stages of production and final products takes place hourly. The final study is carried out before the preparation of the accompanying documentation: passports of finished products. The form is a quality guarantee from the manufacturer.
TAIF-NK is ready to become a guide to the world of VCC for the industry
Being the first, at some points going “by touch”, by trial and error is very difficult — they confirm at TAIF-NK.
“At the time when we decided to build the VCC unit, when this project was being implemented, when commissioning was being carried out, unfortunately, there was no book called 'VCC — fundamentals of design and operation'. Looking ahead a little, I can say that we are currently writing such a book by a team of authors of TAIF and TAIF-NK. If we talk about the original version of the designers' idea and compare it with what happened as a result of all the trial and error, then I probably won't be lying if I say that we have developed a new technology or at least significantly improved. It combines all the processes of suspension hydrocracking, combined hydrocracking, etc. A lot of decisions that were implemented due to objective circumstances in the construction project of the HRCC are unique. This is a huge experience, which, if you build a similar process on VCC, can be implemented already at the stage 'from paper', which will significantly increase the efficiency of operational production, reduce commissioning," says the chief engineer of TAIF-NK JSC.
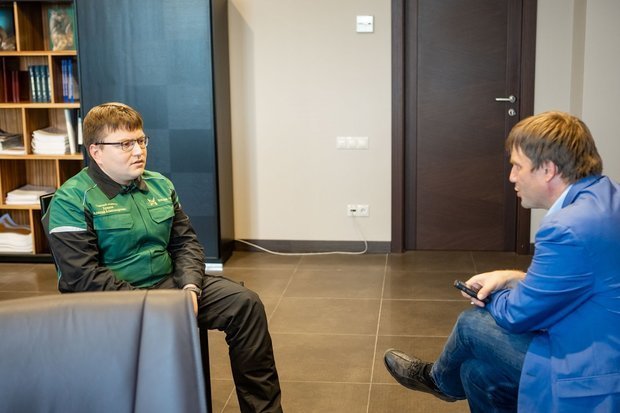
The experience of building and implementing VCC technology is also a product, and it costs a lot and promises to be in great demand in the foreseeable future. Moreover, VCC is the most promising technology that can become a support for the oil refining of the future.
“When light oil ceases to be available, then the time will come for heavy bituminous oil. That time is not far off. I think that in the horizon of the next 10-15 years. And we are actually laying the foundation, the foundation of a huge industry, the industry of processing heavy bituminous oils. This will be VCC technology, and this foundation is being laid here in Tatarstan, at TAIF-NK," Aleksey Khramov allowed himself to look into the near future.
Подписывайтесь на телеграм-канал, группу «ВКонтакте» и страницу в «Одноклассниках» «Реального времени». Ежедневные видео на Rutube, «Дзене» и Youtube.