TAIF-NK: history of Tatarstan petrol
From the first pile to the first petrol — in 2 years
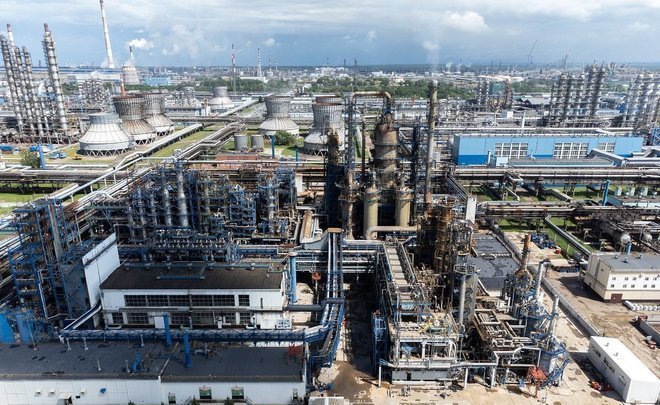
It's hard to believe, but until 2005, the very concept of “Tatarstan petrol” hadn't existed. The republic, having the richest oil reserves, imported automobile fuel from other regions. TAIF Group undertook to improve the situation. About how the first petrol plant in Tatarstan was created and the stages of its formation — read in the continuation of the series of materials of Realnoe Vremya about the history of TAIF-NK's oil refining complex.
TAIF-NK is a full-cycle oil refining complex
In the previous parts of the series, we have already told that the first mentions of Tatarstan oil were heard from the middle of the 17th century and that attempts were made to establish oil refining back in 1753. However, the creation of the first oil refining complex on the territory of the republic began only at the end of the 20th century.
TAIF Group, which created a subsidiary company, TAIF-NK, in 1997, took up the idea of creating its own oil refining in Tatarstan. At the first stage, it had at its disposal only the ELOU-AVT-7 unit leased from Nizhnekamskneftekhim with a design capacity of 6 million tonnes of raw materials a year. However, the young company set ambitious goals for itself — to build a powerful full-cycle oil refining complex in the republic in the shortest possible time, capable, unlike the vast majority of refineries in Russia and the world, to produce the widest possible range of marketable products: from raw materials for petrochemical industries to motor fuels.
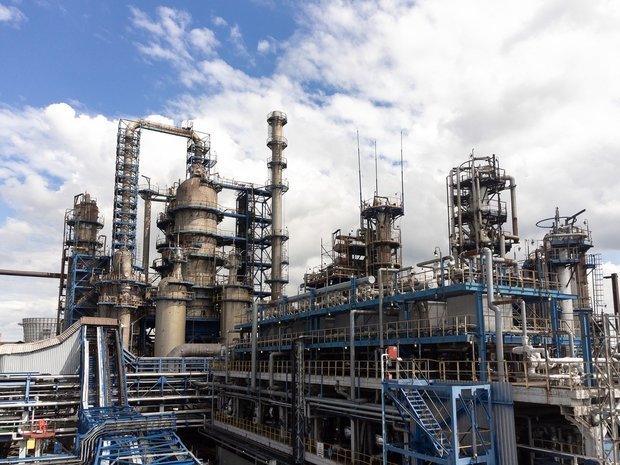
The first task — to ensure a full load of ELOU-AVT-7 and to provide Nizhnekamskneftekhim with sufficient volumes of straight-run petrol — was completed in less than a year. The by-product was high-sulphur boiler fuel.
From the first days since the foundation, TAIF-NK actively invested in the modernisation of the inherited equipment and the construction of new capacities, increasing the volume and conversion rate of heavy Tatarstan oil, striving to maximise the share of light oil products output. The question of the need to build our own gasoline plant, the first in the history of Tatarstan, became acute.
The only one in Russia and the world
In search of an optimal solution for the construction of a gasoline production plant, the specialists of TAIF Group carefully studied the best international and domestic practices, effective technologies. Negotiations were held with the manufacturers of special equipment.
It is worth noting that there have been a lot of offers from large companies, including those known all over the world. However, famous brands also demanded a considerable price for their services. TAIF chose its own path: designing a catalytic cracking gasoline hydrotreating unit, as well as developing formulations and technologies for producing commercial gasoline brands “Normal-80", “Regular-92", “Premium-95". Obtaining certificates and permits to production facilities was entrusted to the VNIIP NP JSC (All-Russian Scientific Research Institute for Oil Refining (Moscow), and the development of the technology of the reactor unit, fractionation of reaction products and the purification of process condensate was carried out by Elistek Engineering PLC (Moscow).
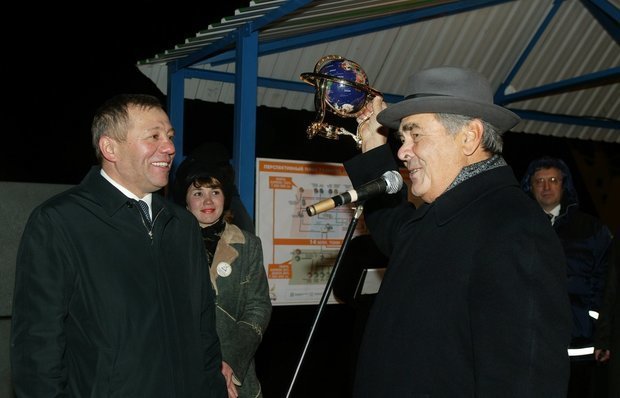
In 2003, the project was launched. The main part of the equipment was ordered from the plants of the Russian Federation and the Republic of Tatarstan. As a rule, 39 calendar months are allocated for the creation of a production facility of this scale — from design to commissioning, but thanks to clear leadership, competent management and concentration of both financial and labour forces of the entire TAIF Group, already in December 2005, with 1,5 times ahead of schedule, the production was put into operation.
Already 2 months later, the plant with a design capacity for processing vacuum gas oil of 1 million tonnes a year gave the first products that fully meet the quality requirements at that time. It was a complete surprise for foreign equipment manufacturers that the production, equal in capacity, fully meets all modern world requirements for the design of technological circuits and hardware design, has reliable protection against emissions and effluents, has a compact location on land and is controlled by modern electronic control and protection systems, that is, in no way inferior to those options what they offered can be realised for an amount less than five times!
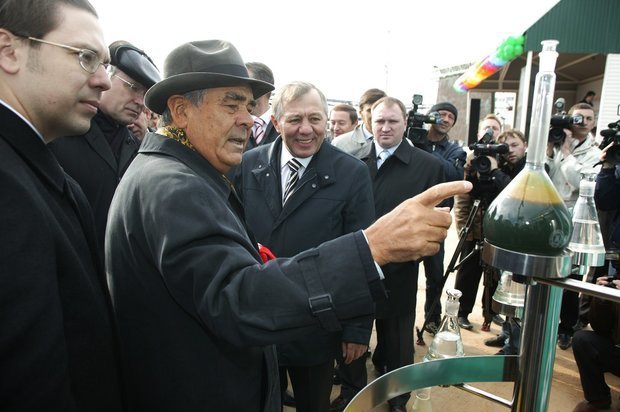
“This is a unique production. Firstly, it is the only catalytic cracking plant in Russia and, accordingly, in the world, built using Russian technology from a Russian designer — VNIIP NP. It was built in 2005, successfully put into operation and currently operates at maximum loads, with the production of gasoline, liquefied gases, a wide range of gasoline components, raw materials for the production of diesel fuel at the refinery," said Aleksey Khramov, the chief engineer of TAIF-NK JSC.
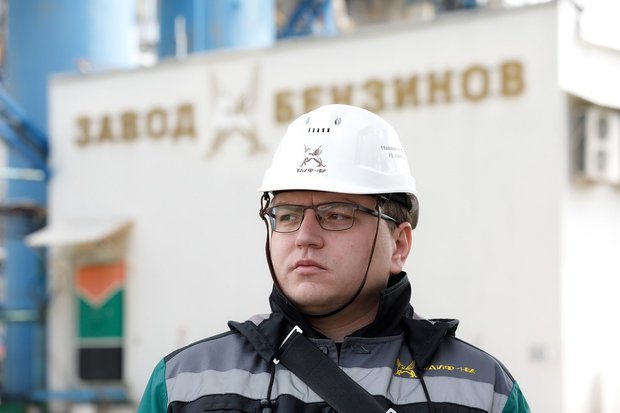
In May 2005, the construction of the second production of the Gasoline Plant began — the gas condensate processing plant with a raw material capacity of 1 million tonnes a year. The development of project documentation was also carried out by domestic specialists — employees of the Samaraneftekhimproekt Institute. A little more than a year after the start of the project, in July 2006, the production gave the first products. The project was led by Vladimir Presnyakov, the deputy director general of TAIF JSC for petrochemistry and oil refining.
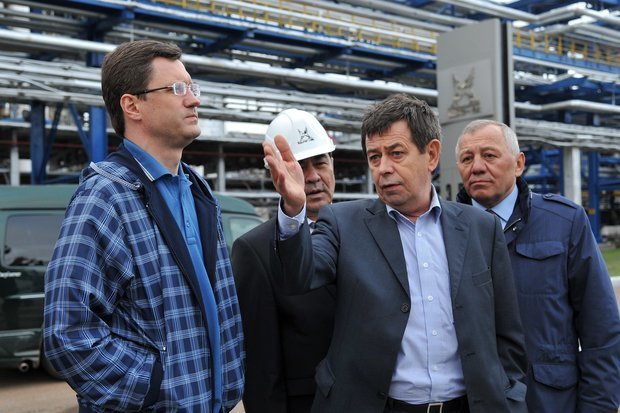
The director general of TAIF JSC, Albert Shigabutdinov, noted: “Presnyakov is 90% responsible for such a successful and effective implementation of such large-scale tasks. These were his ideas and developments. The project manager, thanks to his experience and knowledge, managed to find and implement such an effective solution that no one believed and still does not believe that such a thing is possible, but we did it.”
Evolution of the Gasoline Plant
Striving for the best result is an almost endless process. Maksim Novikov, the director general of TAIF-NK JSC, is sure of this.
“As far as I can remember, all our life we have been building something, achieving some results: either an increase in productivity, or an expansion of the basket of products. Naturally, the whole basket of products has always been and remains high-quality. There were many stages, but we always kept up with the times. As it is now," he said in an interview with Realnoe Vremya.
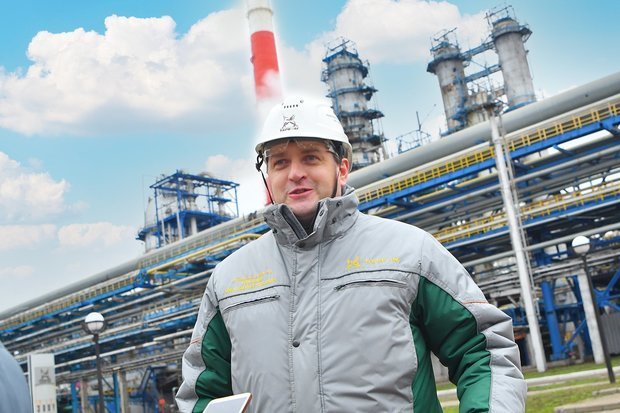
This statement is true for the oil refining complex in general, and for the Gasoline Plant in particular.
And if at the beginning of 2006 — the period of actual industrial production of motor gasoline, its products met the requirements of international standards Euro 2, then at the beginning of 2007 — after the completion of the reconstruction of the desulphurisation unit — the quality of produced gasoline already met Euro 4 standards. In 2008, the corresponding certificate was obtained, the production of Euro 2 gasoline was discontinued.
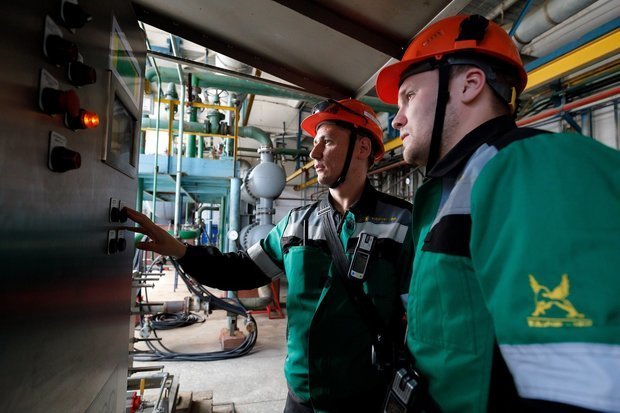
At the Production No. 2 in 2007, the gas condensate processing plant was reconstructed, which made it possible to expand the list of commercial products produced. Technical kerosene was added to straight-run gasoline, diesel fuel, fuel oil, liquefied petroleum gases and kerosene. And mazut has been used as a component of boiler fuel until recently. After the reconstruction, all mazut is used only as raw materials for the installation of catalytic cracking — the heart of the first production of the Gasoline Plant.
In January 2009, another important event took place at the first production of the Gasoline Plant: the commissioning of the esterification unit. TAIF-NK established its own production of high-octane components of commercial gasoline — up to 24,8 thousand tonnes a year of MTBE from isobutylene and up to 152,8 thousand tonnes a year of TAME from isoamylenes.
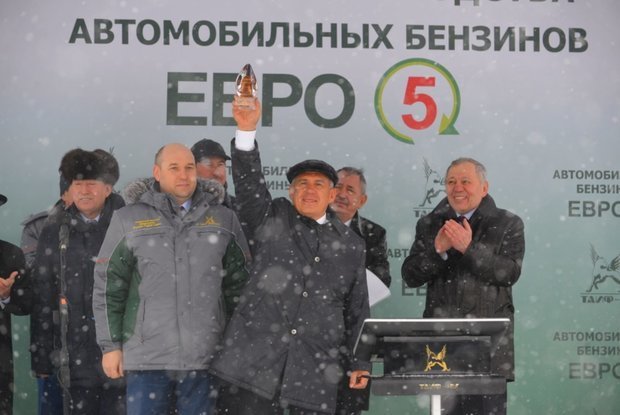
In 2015, ahead of the deadlines set by federal requirements, the TAIF-NK Gasoline Plant completely switched to the production of Euro 5 standard motor fuel.
For information: sulphur content in gasoline mg/kg:
- Euro 2 — up to 500;
- Euro 3 — up to 150;
- Euro 4 — up to 50;
- Euro 5 — up to 10.
In general, environmental issues at the Gasoline Plant, as well as in general for TAIF-NK JSC and TAIF Group, are given great attention throughout their activities. Over the past few years, it has been possible to significantly reduce the environmental burden even more.
Examples were given by the director of the Gasoline Plant, Ilsur Samigullin:
“In 2020, we upgraded the single-stage burners at the gas condensate processing plant into two-stage ones. This allowed us to completely get away from burning mazut as fuel. Mazut itself in the amount of 6 thousand tonnes a year has become an additional raw material for the installation of catalytic cracking. This significantly increased the environmental friendliness of production processes, reducing emissions of sulphur and nitrogen oxides, and additional volumes of raw materials led to an increase in economic effect. In 2022, we transferred all the effluents of purified condensate from the catalytic cracking plant for processing and purification to the refinery plant. Accordingly, discharges into the drains of Nizhnekamskneftekhim PJSC are reduced to zero. In the shipping shop, we upgraded the steam recovery unit, which, when filling gasoline, collects up to 99,7% of vapours.
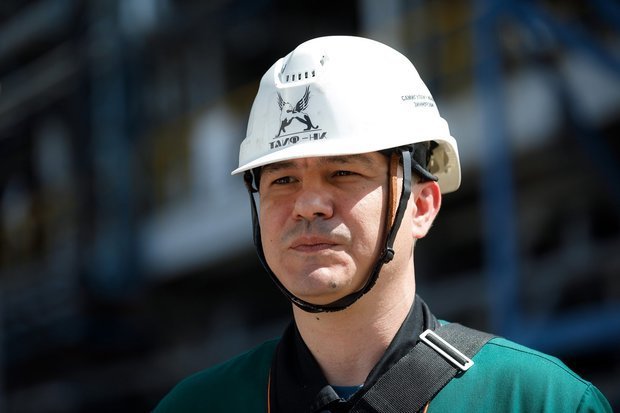
In the future, many more events await the Gasoline Plant: the management of TAIF-NK JSC is already making plans for further modernisation and expansion of production facilities.
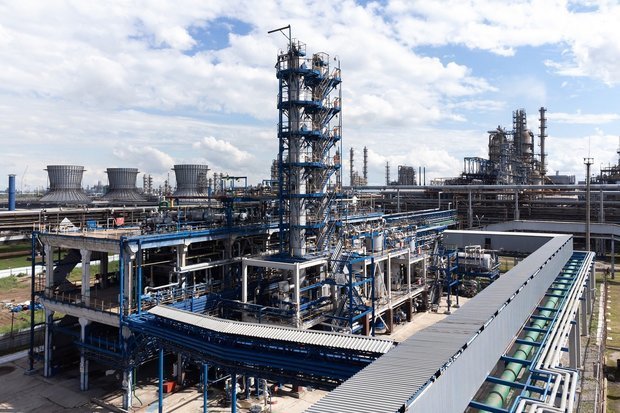
Before and now, and in the future, one of the foundations of success is quality control at all stages of production — from the receipt of raw materials to the shipment of finished products to consumers, including at TAIF-NK filling gas stations of the TAIF Group's own network. This important mission is entrusted to the Gasoline Plant's own laboratory. More than 140 thousand tests and more than 42 thousand analyses of samples of raw materials of intermediate and marketable products are carried out a year. More about what kind of products are produced by the plant, the work of the laboratory and the people who work at this refinery complex enterprise — in the following materials of the series.
Подписывайтесь на телеграм-канал, группу «ВКонтакте» и страницу в «Одноклассниках» «Реального времени». Ежедневные видео на Rutube, «Дзене» и Youtube.